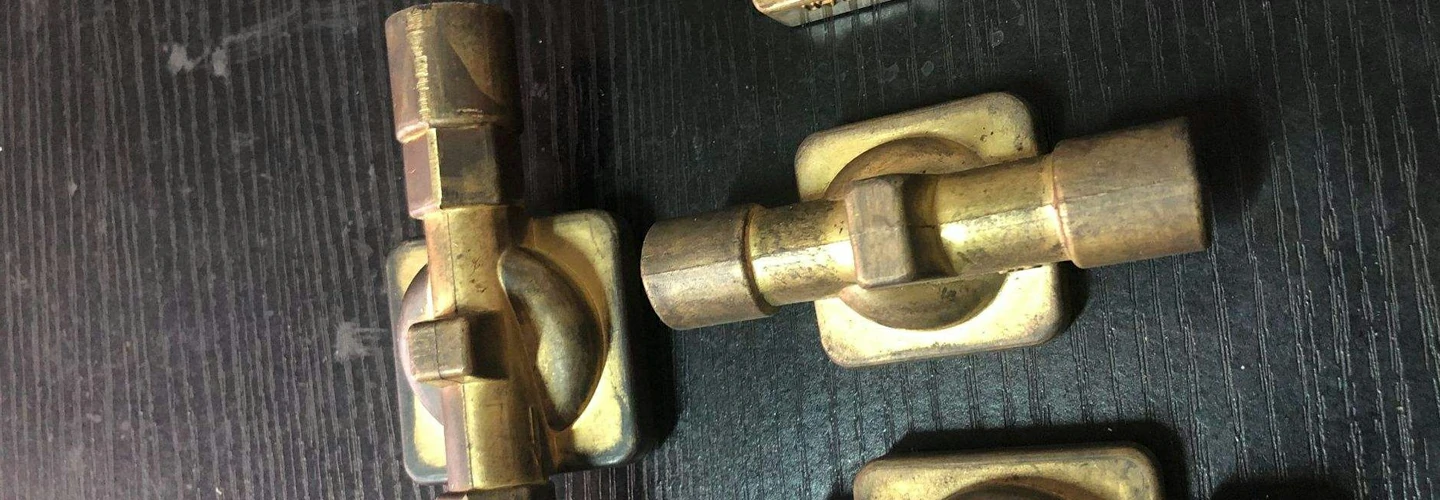
Custom Copper, Bronze, and Brass Forging
Copper alloy has good fluidity, good workability, high strength, strong toughness, good plasticity, wear resistance, corrosion resistance, good thermal conductivity, good electrical conductivity, high mechanical properties, and also has a good decorative effect. Therefore, it is widely used in clocks and watches, decorative materials, electrical and electronic equipment, connectors, heat exchangers, faucets, plumbing, aerospace, shipbuilding, marine industry, nuclear energy, automobiles, rail transit, construction and other industries. The forging temperature range of copper alloy is between 150 and 200 °C. Commonly used copper alloys are brass, bronze and cupronickel.Forging copper alloy(Red Copper/Brass/Bronze) is a process in which a forging product with certain mechanical properties, certain shape and size is obtained by applying pressure to the copper alloy blank by using a forging machine to deform it.
Pintejin provide hand forged copper alloy for the aerospace, marine,automotive , electronic and more industries. Pintejin forging manufacturers copper/brass hand forgings in squares, rectangles, rounds, octagons in any size your job requires. We pride ourselves in working with our customers on every job from one pound parts to 5,000 pound parts. We applies rapid Infrared heating in the process of making copper alloy hot forgings resulting in enhanced physical properties: improved fatigue life, fine grain aluminum metallurgy, and increased hardenability.We uses IR heating technology to reduce energy consumption and lower costs.We provide our customers with contour cuts or special shaped parts to meet their specifications. If your job requires tre-panning or gun drilling just tell us and we will be happy to make the order exactly as you desire.We have perfected our custom copper, bronze, and brass forging processes for over 30 years. As a one-stop-shop for metal parts and assemblies, we strive to provide the custom forgings you need at the competitive prices you want.
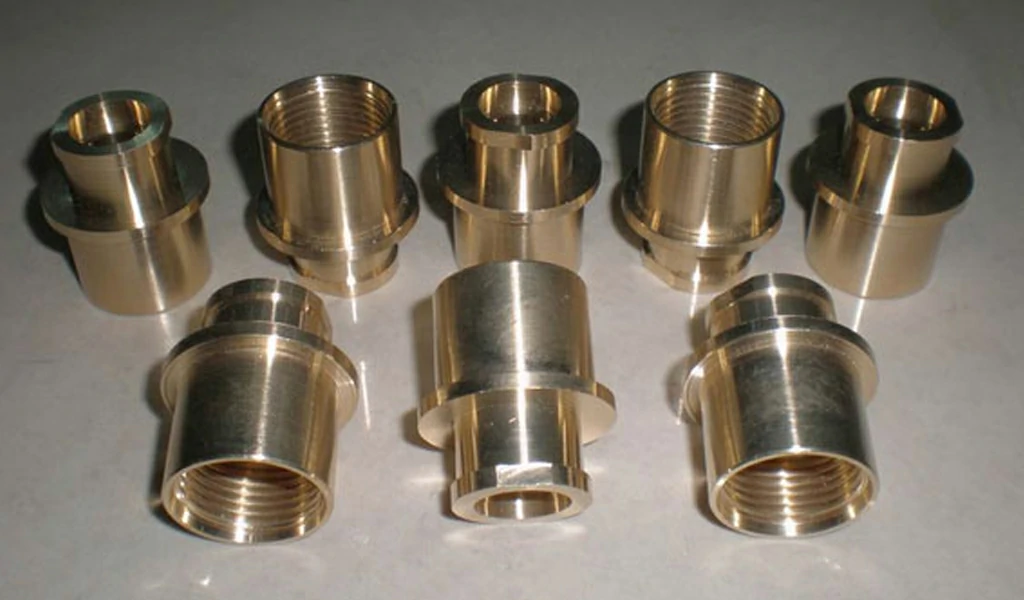
What Is Copper Alloy Forging
What Is Brass Forging?
- Forging brass is the process of applying pressure to the brass billet by using a forging machine to plastically deform it to obtain a forging product with certain mechanical properties, certain shape and size. Forging is one of the two major components of forging (forging and stamping). Through forging, defects such as as-cast looseness produced by brass in the smelting process can be eliminated, and the microstructure can be optimized. At the same time, the mechanical properties of forged brass are generally better than those of castings of the same material due to the preservation of the complete brass streamline.
- The raw state of forged brass material is bar stock, ingot, brass powder and liquid brass. The ratio of the cross-sectional area of brass before deformation to the cross-sectional area after deformation is called the forging ratio. Correct selection of forging ratio, reasonable heating temperature and holding time, reasonable initial forging temperature and final forging temperature, reasonable deformation amount and deformation speed have a lot to do with improving the quality of forged brass products and reducing costs.
- Generally, small and medium-sized forged brass use round or square bars as blanks. The grain structure and mechanical properties of the bar are uniform and good, the shape and size are accurate, and the surface quality is good, which is convenient for mass production. As long as the heating temperature and deformation conditions are reasonably controlled, forged brass with excellent performance can be forged without large forging deformation.
- Defects that are prone to occur in the process of forging brass: overheating and overburning; forging cracks; cutting edges and tearing; when the folded copper alloy is deformed, the surface is easy to wrinkle. Therefore, it is easier to produce folding; coarse grains; stress corrosion cracking.
What Is Red Copper Forging
Brass, Bronze, and Copper Forging Advantages
- High ductility
- Outstanding machinability
- Excellent joining and plating characteristics
- Superior polishing and finishing characteristics
- Non-magnetic properties
- Non-sparking characteristics
- Attractive solid colors, not just surface
The Production Process Of Wrought Copper Sculpture
- Clay manuscript production: Clay sculpture production is an important link in the production process of wrought copper sculpture, and it is the main step to determine the basic shape and style of the sculpture. It needs to be approved by Party A. After the small manuscript is determined, the sculpture mud manuscript can be enlarged. make.
- Mold-turning production: After the mud draft is confirmed by Party A, the mold can be turned (usually made of FRP draft). Since the forged copper sculpture needs to be repeatedly forged and moved, the FRP draft requires a high thickness and a strong inner skeleton. , if this requirement is not met, the mold may crack during the forging process, which will affect the production progress and production effect of the sculpture.
- Cutting and forging: Line and divide the finished FRP draft, which is convenient for copper plate cutting. Electric scissors or plasma cutting machine can be used for cutting copper plate. After cutting, it can enter the forging part.
- Assembly: When the forging reaches a certain stage, the sculpture assembly process can be entered. The forged copper plates are assembled in sequence according to the FRP draft. The places with small gaps can be welded with a argon arc welding machine, and when the gaps are large, fire welding can be used. For splicing, the craftsman is required to process in strict accordance with the FRP draft, the splicing is not deformed and distorted, and the details are handled delicately. Here, attention should be paid to the strength of the internal skeleton of the sculpture and the firmness of the nodes.
- Coloring treatment: After the overall production of the forged copper sculpture is completed, in order to facilitate the coloring effect and adhesion of the forged copper sculpture, it is polished and trimmed with a fine grinding wheel as a whole. Coloring is the most important part of wrought copper sculpture. It must be successful at the first time. If it is not handled properly, it will become the biggest failure of the sculpture. It is time-consuming and laborious to make changes.
- On-site installation: The wrought copper sculpture should be prevented from bumping during transportation and hoisting. Attention should be paid to the connection and reinforcement of the embedded parts in welding, and the wind resistance and anti-damage strength of the sculpture. Finally, the welding points should be treated with complementary colors.
The copper forging process gives full play to the ductility of the metal sheet to produce volume changes in space. The following is a detailed description of the process treatment in the forging copper casting process.
1. Treatment of metal technology
The copper plate should choose red copper (both pure copper, also known as red copper) with a thickness of more than 1.2mm. High temperature annealing is required during forging, and forging is started after cooling. In this way, the flexibility and ductility of copper can reach the best state. When forging high relief, calcination and annealing must be carried out, and so on. Only after many times can the relief forging hammer reach the ideal height. This treatment can prevent work hardening and fracture, and is also conducive to further extending and deforming the copper plate to reach the ideal height of the relief forging hammer.
2. The craftsmanship of chisel shape (known as saving by craftsmen)
First, copy the created artwork in equal scale, fix it on a copper plate with latex, and then put it on the ground with a special offset plate to chisel (also called through draft). Use various chisel (chisel-shaped tools) to accurately chisel the line drawing on the copper plate according to the drawing, and then re-level the relief copper plate with a rubber hammer, wooden hammer, wooden beat (square wood), etc. Chiseling is an important link, because the accuracy of the shape directly affects the next forging process. After chiseling, a special offset plate (called modeling paste in art schools) must be chiseled with large ups and downs.
3.The forging process
This process is the most important, it directly determines the success or failure of the relief. There are two types of forging: if the frame is small, beating directly on the desk padded with modeling paste. This is a technically demanding process, and the entire copper plate is repeatedly forged and struck. Determine the height, depth, and level of the relief. After the rough forging procedure is completed, the finer forging must be followed up to adjust the subtle changes of the relief and the upper and lower relationship of the hierarchical structure. At the same time, the copper plate should be calcined and annealed in time to avoid breaking the copper plate.
In the process of "starting up", it should not be lifted too high at once, otherwise it will break. This has to be repeated many times. Each time "starting up" must be heated with acetylene at high temperature to soften it (increase the elongation of the copper plate). properties), cooled and then hammered and forged.
4.The process of shaping (also known as finding thin)
It is to refine and correct the overall shape of the forged relief to make the image fine and perfect. You can also use the sculptural paste to fill the negative (both the back) of the figure, and then use a small chisel to beat the detailed shape of the relief to gradually deepen. The details depict from the whole to the part, and then from the part to the whole, and constantly adjust the primary and secondary relationship and physical structure of the relief to make it linear and strong, clear in structure, and vivid in outline and image. According to the form and content of relief creation, in the process of forging. In the middle, the process texture of hammering and forging can be preserved, making the relief works more artistic appeal and tension.
5.Grinding and polishing process
The wrought copper relief after shaping may leave defects such as solder joints and rough carvings during the production process, so the relief must be ground and polished. For relief grinding, rough grinding first, and then grinding with various files and gauze, is also a process to further make the whole clearer. After grinding, use a polishing machine to further remove all traces of work on the raised surface, so that the raised surface is smooth and beautiful.
6.Wrought copper relief surface coloring and protection process
The processing technology of coloring and protecting the surface of copper plate is very complex and diverse. The surface treatment of relief works should be selected according to the content and style of the work.
Steel Forging Part In China Steel Forgings Suppliers
As a professional forging manufacturer, Pintejin has extensive forging expertise, such as hot forging, warm forging and cold forging, as well as design and engineering expertise. With our unparalleled manufacturing capabilities, we strive to challenge long-term practices to constantly exceed the established framework constantly.We have many years of experience in manufacturing a variety of high-performance, critical and safety components.
-
Forging 5083 5052 6061 7075 2A12 Aluminum Flange
-
Aluminum Alloy Forged Mountain Bike Shoulder Cover
-
Aluminum Hot Die Forging Automotive Parts
-
Aluminum Alloy Die Forged Bike Folder Shoulder Cover V Brake Parts
-
Aluminum Alloy Hot Forged Bike Transmission Hook
-
Die Forged Packing Belt Connecting Mesh Ring
-
Forged Carbon Steel Special-Shaped Split Flange
-
Custom Forged Special-Shaped Hinge Spade Pins
If you are looking for Metal Forging Service,Pintejin is ready to give them to you! With us, you will have the opportunity to make your custom Hot forging parts, cold forging parts,machined parts, prototype production easy and less hassle. If you want to avail our service, call us now and get a metal forgings quote!