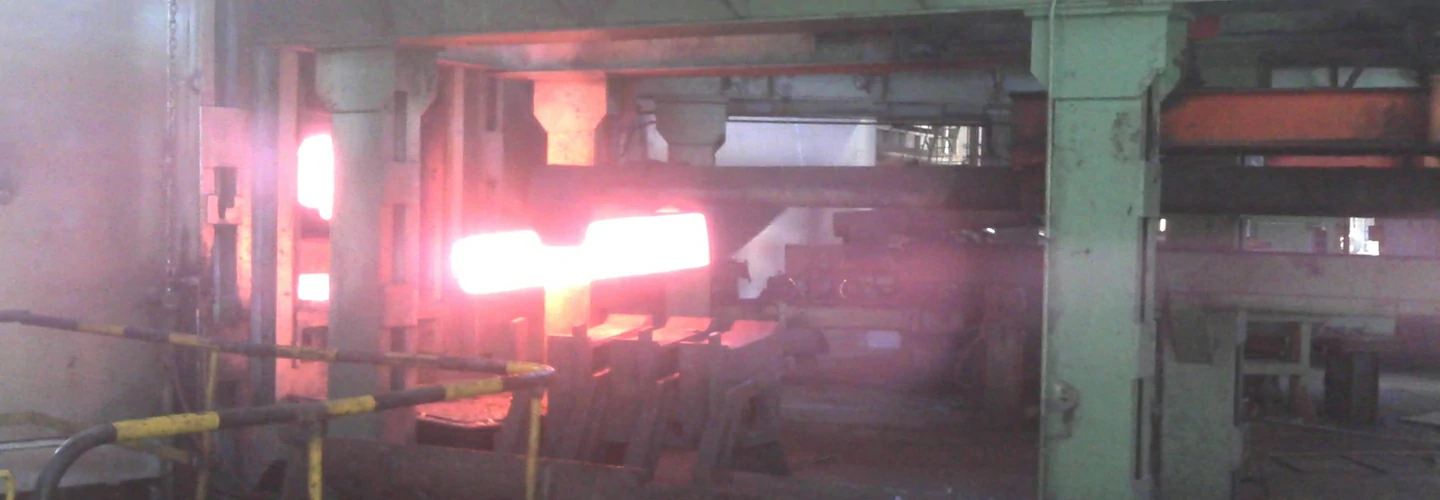
Die Forging Factory In China
Die forging is one of the forging types for small or medium metal components. Compared to the open die forging, the die forging (said also Closed die forging and hot drop forging) can achieve more complex geometries, very much close to the dimensions of the finished component.Die Forging is a general term for dies used for bulk forming of metals in a hot or cold state. Due to the different working characteristics of various die forging equipment, the structure of the forging die is also quite different, and the design of the die cavity is also slightly different. For a perfect forging die design process, the first consideration should be: to be able to obtain forgings that meet the requirements of dimensional accuracy and good structure and properties, and at the same time to meet the requirements of productivity; secondly, it should also be considered that the forging die should have sufficient strength and high life. , and simple manufacturing, installation, adjustment, maintenance and other requirements. Therefore, a comprehensive analysis should be carried out when designing a forging die.
Die Forging manufacturing is the first step to forging parts. Our engineers will design forging dies based on the drawings of new forgings. The design of the forging die depends on the processing steps, the nature of the workpiece material, the flow stress, and the working temperature, among other factors.
Generally speaking, we need to accurately calculate the volume of the blank to avoid under-filling or overfilling. The choice of parting line (referring to the line where two molds intersect) is also very important. Sometimes for forged parts, there are multiple options to choose the parting line. Note that the parting line ensures the flow of materials is divided evenly. In other words, if there is no way to determine the parting line, forging is not feasible.
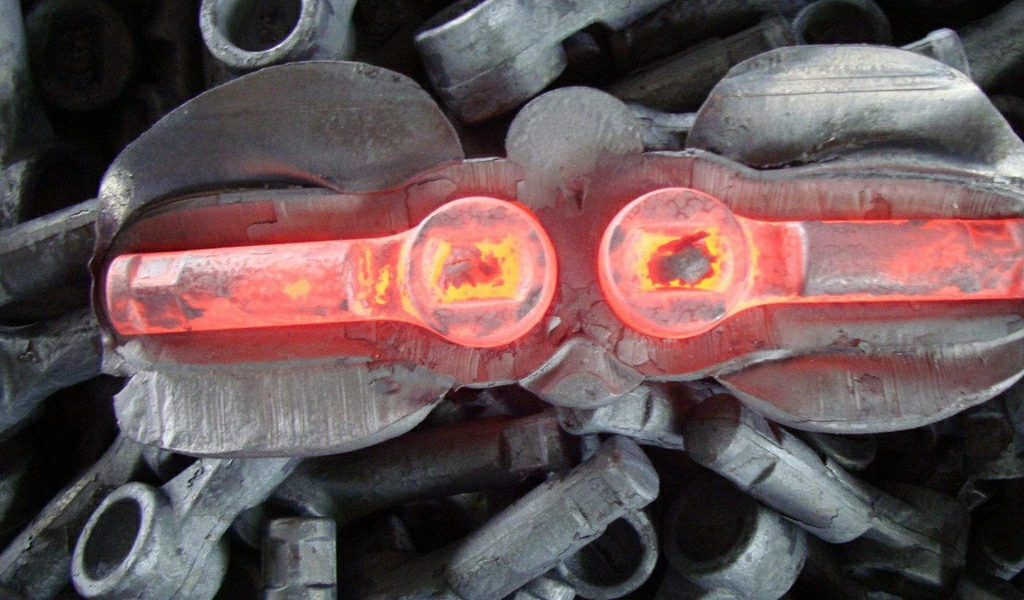
What Is Die Forging
The Features Of Die Forging
The process of forging and forming a metal blank with a forging die on a die forging hammer or press. The die forging process has high production efficiency, low labor intensity, accurate dimensions, small machining allowance, and can forge forgings with complex shapes; it is suitable for mass production. However, the cost of the mold is high, and special forging equipment is required, which is not suitable for single-piece or small batch production.
- The shape of the forgings can be complex due to the presence of a die bore to guide the flow of metal.
- The forging streamlines inside the forging are distributed according to the contour of the forging, thereby improving the mechanical properties and service life of the parts.
- Simple operation, easy to realize mechanization and high productivity.
The Classification Of Die Forging
The Classification According To The Equipment Used
According to different equipment, die forging is divided into hammer die forging, crank press die forging, flat forging die forging, friction press die forging, etc. The equipment for die forging on the hammer is a die forging hammer, usually an air die forging hammer. For forgings with complex shapes, they are first formed in the blank die cavity, and then forged in the forging die cavity. According to the structure of the forging die: a forging die with a burr groove to accommodate excess metal is called a free forging die; on the contrary, a forging die without a burr fly groove to accommodate excess metal is called closed die forging. Forming directly from the original billet is called single die forging. For forgings with complex shapes, the same forging die needs to be preformed in several steps, which is called multi-die forging. Precision die forging is developed on the basis of die forging, and can forge some complex shapes with high dimensional accuracy. High parts, such as: bevel gears, blades, aerospace parts, etc.
Forging dies process metals at high temperature, and the working conditions are poor. They need to withstand repeated impact loads and alternating cold and heat, resulting in high stress. There is also a friction effect when the metal flows. Therefore, the mold should have high strength, hardness, wear resistance, toughness, oxidation resistance, thermal conductivity and thermal crack resistance under working conditions.
The Classification According To The Type Of Forging Die
The forging die is used to deform the blank into a forging according to the specified shape and size. Forging dies are generally composed of upper and lower modules. There are die grooves on the module, and the number and shape of the die grooves are determined by the forging process. There are two types of forging dies: integral die and insert die, and integral die is divided into single die groove and multi die groove. Due to the difference of die forging equipment, forging dies can be divided into hammer dies, screw press dies, crank press dies, flat forging dies and hydraulic press dies. Forging dies with hammers are more complicated. According to the size of the production batch, the hammer forging die is mostly used in the mass production of the integral multi-slot die; the forgings are varied in variety and the batch is small, and the integral single-slot die or the insert die is mostly used.
- Integral single slot die: This type of forging die generally has only one final forging die slot. This forging die has a simple design, small module size, short manufacturing cycle, low cost and simple operation. The disadvantage is that it is limited by comprehensive factors such as raw material utilization rate and low production efficiency in mass production, and the adaptability is poor. The single-slot die generally uses the original bar material, and forges simple-shaped forgings such as circular parts or rods with little change in cross-section in the final forging die groove.
- Overall multi-slot die: This die is not only provided with final forging die grooves, pre-forging die grooves, but also multiple die grooves such as blank-making die grooves. It has the advantages of high production efficiency and good forging quality. It is suitable for the production of forgings with complex shapes and large production batches, and is widely used by forging manufacturers.
- Insert die: The final forging die groove or part of it that is easy to wear is made of high-quality die steel as an insert, and it is installed on the module made of ordinary steel by wedge iron or hot sleeve method (as shown in Figure 1 on the right). ) The reliability of the die fastened by the wedge iron or shrink fit is poor, which has a certain influence on the dimensional stability of the forging. Therefore, when mass-producing complex forgings, it is still desirable to use a forging die with a monolithic structure.
How To Make Forging Die
The forging die for die forging consists of two upper and lower modules. The die cavity is the working part of the forging die, and the upper and lower dies are half each. It is fixed on the hammer anvil and the worktable with dovetail and wedge; and it is guided by a lock or guide column to prevent the upper and lower modules from being dislocated. The metal blank is deformed according to the shape of the die cavity.
The process of die forging is billet making, pre-forging and final forging. The cavity of the final forging die is determined according to the size and shape of the forging, plus the allowance and deviation. Die forging is generally divided into two types: open die forging and closed die forging: there is a burr groove around the die cavity of open die forging, and the excess metal flows into the groove after forming, and finally the burrs are removed; closed die forging only has a small edge at the end. Burr, if the blank is accurate, there can be no burr.
The Design Steps Of Forging Die
- According to the shape, size and performance requirements of the machine parts to be manufactured and the selected process plan, determine the machining allowance, parting surface, draft angle, fillet radius, punching and skin and dimensional tolerances of the forgings, etc. , draw the forging diagram, and calculate the total volume of the forging.
- Calculate the shape and size of the corresponding die cavity for each process step according to the set work step, first forge the die cavity, followed by the pre-forging and billet die cavity and the specifications of the billet, and draw a detailed work step diagram. Finally, the shape and size of the die cavity of the forging die are determined according to the working step diagram.
- Calculate the tonnage of the forging pressure, select the forging equipment, arrange the position of the die cavity according to the working space and structure of the equipment, carry out the overall design of the forging die parts, and select the dimensions of the relevant parts and the forging die materials and technical conditions. Drawing of the components and parts of the forging die
Design Point Of Forging Die
According to the deformation characteristics of the metal during die forging, the forging die cavity can be divided into four types: billet (including bending) die cavity, pre-forging die cavity, final forging die cavity and cutting forging die cavity. When designing the die cavity for billet making, the structure of the die cavity should be ensured, so that the shape of the billet can be gradually changed according to the process requirements, and a billet with a suitable section size and a smooth surface can be obtained, so as to improve the stress state of the pre-forging and final forging die cavity and prolong its life. . On this basis, the requirements of die strength, forging die processing and easy operation during forging should also be considered. Therefore, the following points must be comprehensively considered:
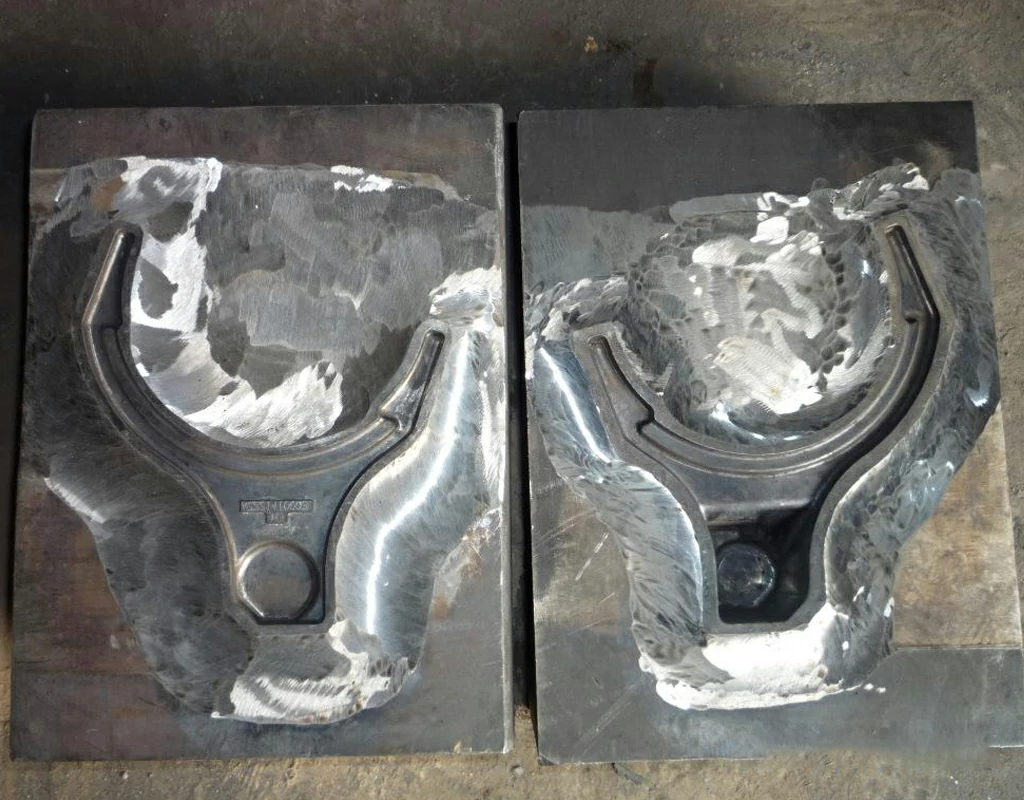
- When the shape of the die cavity or the parting surface of the forging die is asymmetric, the forging will generate a horizontal thrust, which is easy to displace or damage the die. It should be designed in a symmetrical shape as much as possible; for forgings with asymmetrical shapes (especially curved forgings), the integrity of the die cavity should be guaranteed as much as possible.
- It should be ensured that the centroid of the horizontal projection of the final forging die bore (including the flash edge) coincides with the center of the hammer rod (see figure (a) below). When there are pre-forging die bores, they should be arranged as shown in Figure (c).
- The parting surface should be selected as flat as possible to make it easy to manufacture.
- In order to facilitate the removal of forgings from the die cavity, the die forging slope is provided on the sidewall of the die cavity. Generally, the inclination of the inner die forging is larger than that of the outer die forging (see Figure 3 below).
- Appropriate arc transitions should be adopted for the corners of die forgings to facilitate the forming of forgings and improve the strength of the die.
- Narrow and high ribs or thin and wide parts on the forgings are difficult to deform during die forging, and are prone to folding, so attention should be paid to the design.
- The structural dimensions of the flash bridge part and the bin part are related to the difficulty of forming the forging, and should be considered according to the specific shape of the forging. Generally, the width of the bridge is 8~14mm, and the width of the warehouse is 22~40mm.
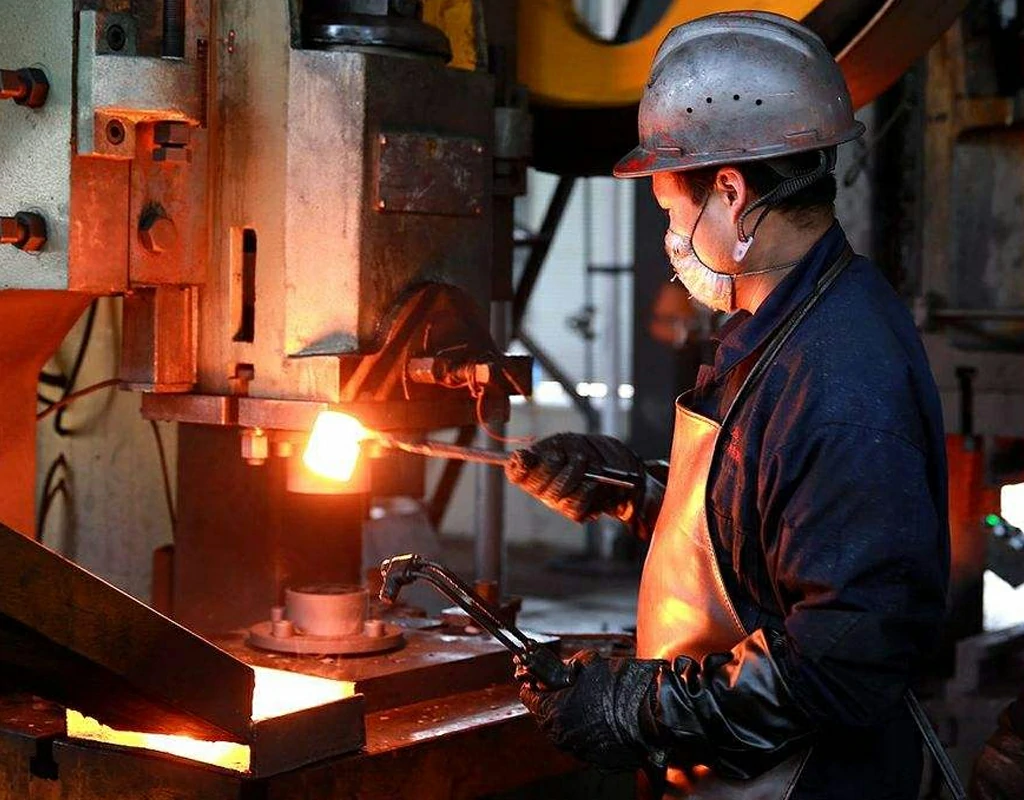
The Material Of Forging Die
During die forging, the die bore is in contact with high temperature forgings for a long time, and the temperature is as high as 200~300℃. The temperature of the thinner parts such as the corners or raised parts of the cavity is even as high as 500~600℃. In addition, the corners of the die cavity have to withstand the strong impact force generated by the blow and the explosive combustion of the coolant, and the working conditions are very harsh. Therefore, forging die materials are required to have the following properties: high heat resistance and wear resistance; good impact toughness; easy to heat treatment, not easy to deform; good cutting performance during machining.
The commonly used forging die material is 5CrMnMo or 5CrNiMo, and other alternative materials can also be selected for small batches of forgings
If you are looking for Metal Forging Service,Pintejin is ready to give them to you! With us, you will have the opportunity to make your custom Hot forging parts, cold forging parts,machined parts, prototype production easy and less hassle. If you want to avail our service, call us now and get a metal forgings quote!