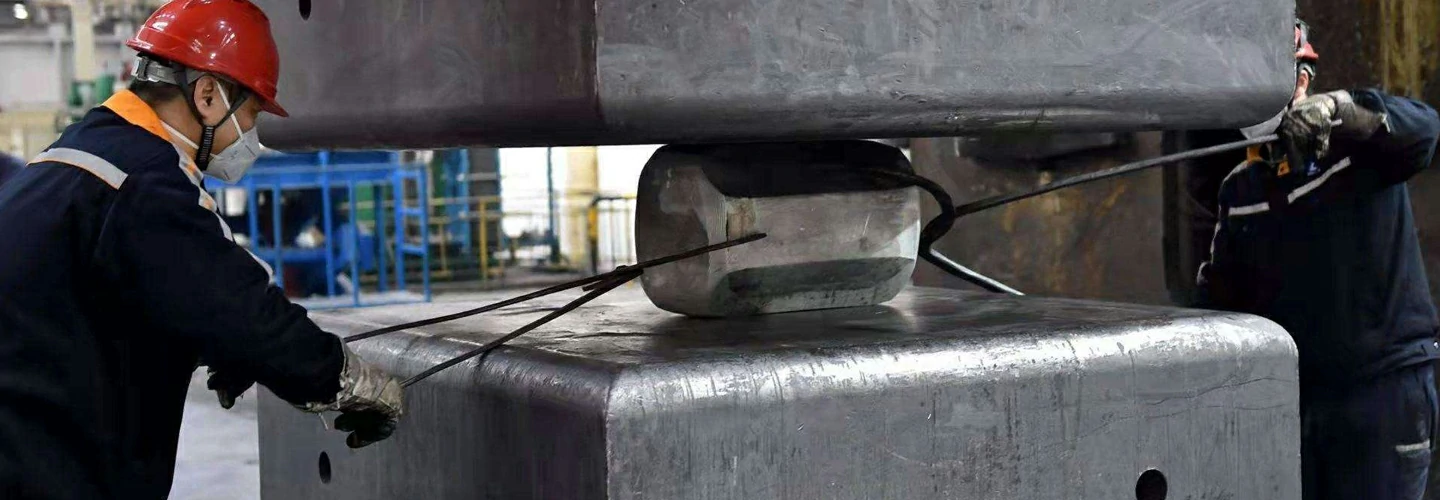
Aluminum Forging
Aluminum forging is a processing method that uses a forging machine to apply pressure to an aluminum billet to plastically deform it to obtain a forging with certain mechanical properties, certain shape and size. It is one of the two major components of forging (forging and stamping).
Pintejin is ISO 9001:2015 custom manufacturer of aluminum forgings.Aluminum grades worked with include 1100, 2011, 2014, 2017, 2024, 3003, 5005, 5052, 5086, 5657, 6013, 6020, 6061, 6063, 6101, 6262, 7050 and 7075. Various capabilities include turning, molding, casting, prototyping, assembly, coating, painting, anodizing, laser marking, engineering and warehousing. Automotive, agricultural, electronics, lighting, marine, medical, telecommunications and other industries served. Specializes in small to large production runs. We provide a full complement of post-forging processes to add further value to forged aluminum parts. To prepare custom forged aluminum parts for secondary machining and assembly, Pintejin’ plants have in-house heat treating capabilities. We offer a variety of surface finishing processes including chemical, vibratory, and shot-blast. Additional services such as anodizing, painting, powder coating, polishing, design assistance, and more, are available to give more complete parts at a lower cost.From high-precision, functional parts to decorative elements,Pintejin can produce most any forged aluminum part you can imagine.
Our capabilities include prototypes or one-offs, small runs, full production quantities and just-in-time inventory supply for long term contracts. Some of the products we forge and processes we use for aluminum forgings include:
- Flat bar blocks up to 80″ width and 10,000 lbs.
- Cylinders and sleeves up to 64″ maximum O.D. and 84″ maximum length
- Discs and hubs up to 80″ diameter and 10,000 lbs.
- Rolled, hand forged or mandrel forged rings up to 80″ maximum O.D. and 65″ maximum length
- Rounds, shafts and step shafts up to 192″ maximum length and 10,000 lbs.
- Forged-in steps or contours to reduce finish machining time and material waste
- Quenching and tempering, normalizing, or annealing of forgings.
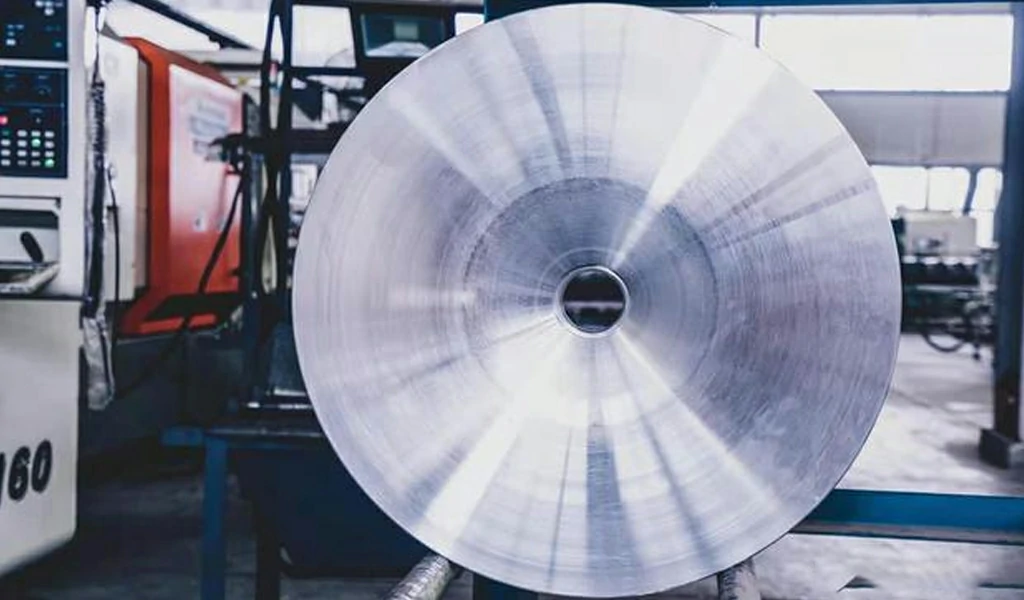
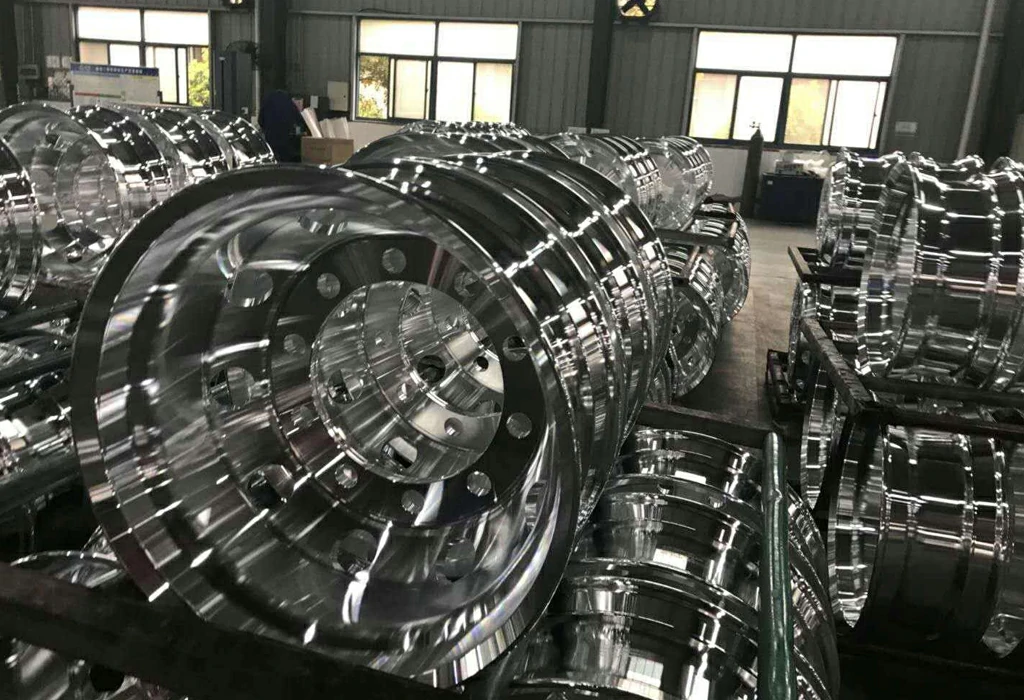
What Is Aluminum Forging
Aluminum Forging VS Aluminum Casting
Through forging, defects such as as-cast looseness produced in the smelting process of aluminum can be eliminated, and the microstructure can be optimized. At the same time, due to the preservation of the complete metal streamline, the mechanical properties of forgings are generally better than those of castings of the same material.
Casting generally adopts vertical or horizontal water-cooled semi-continuous casting method. In order to improve the ingot structure and surface quality of vertical casting, electromagnetic crystallization grooves, short crystallization grooves and hot top casting methods have also been developed (see solidification of metals).
The water-cooled semi-continuous casting method is to introduce the liquid metal into the water-cooled crystallizer through the launder, so that the liquid metal is cooled to form a solidified shell, which is pulled by the base of the casting machine or evenly lowered by its own weight to come out of the crystallizer to form a billet.
Process parameters vary widely due to alloy composition and billet size. Generally, the casting speed and cooling speed should be increased as much as possible, and the height of the crystallization tank should be reduced. The casting temperature is usually 50-110°C higher than the liquidus of the alloy. In addition, the continuous casting and rolling process of aluminum strip has also been developed.
How To Make The Perfect Aluminum Forged Wheel
If you want to do a good job of the wheel hub, the raw material is very important
To build a high-quality wheel, the first thing to do is aluminum. We know that the current mainstream processes of wheel hubs are divided into casting and forging. Casting, as the name suggests, is made of aluminum alloy melted into liquid and cast into molds. Due to the large batches of finished products, it is widely used in mainstream production vehicles; while forging is formed by forging aluminum ingots and then entering CNC. The machine tool is used for modeling. The finished product has high hardness, high density and strong customization properties. It is often found in the top models of luxury and high-performance car brands.
Obviously, there is a fundamental difference in how cast and forged wheels are formed. Because of the different molding methods, the selected aluminum materials are naturally different. The A356.2 series aluminum alloy selected for the cast wheel hub is mainly characterized by strong fluidity, corrosion resistance and good air tightness; while the 6061 series aluminum alloy selected for the forged wheel hub is mainly characterized by high strength and toughness, corrosion resistance, material Dense and defect-free and easy to polish and color, the paint surface effect is good.
From this comparison, it can be seen that the essential difference between A356.2 and 6061 series aluminum alloys lies in strength and toughness. Casting wheels are first melted and then formed, which requires strong fluidity of aluminum, resulting in a significant gap between the strength and toughness of the finished product compared with forging. Of course, as far as most models are concerned, the performance of the real cast wheels can be fully handled, but for the occasional intense driving and driving demands of high-performance vehicles, as well as the relatively harsh and complex road conditions, forged wheels are the best choice. Second choice.
Choosing the right aluminum alloy model is only one of the raw material elements. The reason why forged wheels are mixed in quality and prices vary widely, the main reason is the cost of aluminum.
- Raw material cost. Recycled aluminum is an aluminum alloy or aluminum metal obtained by remelting and refining scrap aluminum alloy materials and scrap aluminum or aluminum-containing waste. The primary aluminum is pure aluminum extracted from the aluminum ore obtained by mining aluminum ore through the electrolytic cell. Compared with recycled aluminum, it has stronger strength, hardness, toughness, oxidation resistance and longer service life, but the cost of primary aluminum is about three times that of recycled aluminum. Therefore, many manufacturers use a large amount of recycled aluminum as raw materials to impact the forged wheel market with low quality and low price.
- Processing cost. The full name of forged wheel aluminum alloy is 6061-T6. As mentioned above, 6061 is an aluminum alloy model, and T6 means that the aluminum alloy has undergone heat treatment. This part of heat treatment mainly plays a role in improving the strength and hardness of aluminum alloys, which is similar to the quenching process of steel. However, some manufacturers will omit this important step to further reduce costs, and the safety performance of aluminum alloys will naturally be greatly reduced.
Making good use of raw materials is only the first step in creating a perfect forged wheel. Next, the precision of the machining of the wheel in the CNC machine tool is equally important.
The Characteristics Of Aluminum Forgings
- Low density, only 34% of steel forgings and 30% of copper forgings, it is an ideal material for lightweight;
- It has high strength, high stiffness, high elastic modulus and high fatigue strength. It is suitable for key stress components with high lightweight requirements, and its comprehensive performance is much higher than other materials;
- The aluminum alloy has good plasticity and can be processed into various high-precision forgings with complex shapes. The machining allowance is small, only about 20% of the machining allowance of the aluminum alloy drawing thick plate, which greatly saves man-hours and costs;
- The internal structure is fine, uniform and defect-free, and its reliability is much higher than that of aluminum alloy castings and die castings, and also higher than other material castings;
- Aluminum forgings have good corrosion resistance, thermal conductivity and non-magnetic properties;
- The surface is smooth and beautiful, with good surface treatment performance, beautiful and durable.
Due to the decline in the cost of aluminum materials, the improvement of performance, and the expansion of varieties and specifications, its application fields are becoming larger and larger. Mainly used in aerospace, transportation, automobile, electronic communication, petrochemical, mechanical and electrical fields.
How To Improve Raw Materials Forging Utilization Rate?
There are a wide range of forgings, which can be divided into various grades of steel and high-temperature alloys, as well as non-ferrous metals such as aluminum, magnesium, titanium, and copper; at the same time, they can also be processed into various specifications of bars, profiles, and domestic materials suitable for my country’s resources. There are materials from abroad.
Most of the forging materials have been included in the national standards, many of which are new materials developed, tested and promoted. We all know that the quality of products is often closely related to the quality of raw materials, so forging workers must have the necessary material knowledge and be good at selecting the most suitable materials according to the process requirements.
Feeding and feeding are one of the important links to improve the material utilization rate of aluminum forgings and realize the refinement of blanks. Excessive material is not only wasted, but also increases cylinder wear and energy consumption. If the blanker does not leave a little excess, it will increase the difficulty of process adjustment and increase the scrap rate. In addition, the quality of the blanking end face will also affect the process and quality of the forging.
The purpose of heat treatment is to reduce the deformation force of the forging and improve the plasticity of the metal. But heating can also cause a series of problems, such as oxidation, decarburization, overheating, overburning, and so on. Precisely controlling the final forging temperature of forgings has a great influence on the structure and properties of the product.
Burner heating has the advantages of low cost and strong adaptability, but the heating time is long, it is easy to produce oxidation and decarbonization, and the working conditions also need to be continuously improved. Inductive heating has the advantages of fast heating and less oxidation, but it has poor adaptability to changes in product shape, size and material.
Forging is formed under the action of external force. Therefore, correct calculation of deformation force is the basis for selecting equipment and performing mold inspection. In terms of optimizing the process and controlling the microstructure and properties of the forging, the stress-strain analysis inside the deformed body is also essential.
The cost of forging production materials in the Central Plains generally accounts for 50% to 70% of the production cost of forgings. Saving raw materials is the main means to reduce the production cost of forgings.
Try to change the cutting material to cutting or precision cutting, develop new precision cutting methods and equipment, promote the development of band sawing machines, and develop new high-speed circular saw blades or high-speed circular saws with bimetallic edge circular saw blades. machine. Replacing some sawing machines is the main measure to improve the blanking productivity of aluminum forgings, reduce blanking losses and save raw materials.
The Advantages Of Automotive Aluminum Forging
- Added directional strength: During automotive aluminum forging, the expected, uniform grain size and flow characteristics can be obtained by strictly controlling the mechanical deformation of the heated metal. Automotive aluminum forgings are also often pre-machined to improve dendritic structure and eliminate voids. This translates into excellent metallurgical and mechanical quality and provides higher directional toughness in the final product.
- Building Structural Strength: Free forging provides structural integrity unmatched by other metalworking methods. Forging eliminates internal voids and air pockets that can weaken metal parts. Alloys or non-metals are dispersed during forging to provide good chemical uniformity. Predicted structural integrity reduces workpiece inspection requirements, simplifies heat treatment and machining, and ensures optimum workpiece performance under field loading.
- Impact Strength: Components can also be forged to meet nearly all stress, load and impact requirements. Correct valley flow direction ensures maximum impact strength and fatigue resistance. Using automotive aluminum forging technology, the section thickness and total weight can be reduced without affecting the quality of the whole piece.
- Metallurgical Specifications: Alloy selection, part configuration, thermal machining and post-forming processes all affect metallurgical properties.
Metal Forging Part In China Metal Forgings Suppliers
As a professional forging manufacturer, Pintejin has extensive forging expertise, such as hot forging, warm forging and cold forging, as well as design and engineering expertise. With our unparalleled manufacturing capabilities, we strive to challenge long-term practices to constantly exceed the established framework constantly.We have many years of experience in manufacturing a variety of high-performance, critical and safety components.
-
Forging 5083 5052 6061 7075 2A12 Aluminum Flange
-
Aluminum Alloy Forged Mountain Bike Shoulder Cover
-
Aluminum Hot Die Forging Automotive Parts
-
Aluminum Alloy Die Forged Bike Folder Shoulder Cover V Brake Parts
-
Aluminum Alloy Hot Forged Bike Transmission Hook
-
Die Forged Packing Belt Connecting Mesh Ring
-
Forged Carbon Steel Special-Shaped Split Flange
-
Custom Forged Special-Shaped Hinge Spade Pins
If you are looking for Metal Forging Service,Pintejin is ready to give them to you! With us, you will have the opportunity to make your custom Hot forging parts, cold forging parts,machined parts, prototype production easy and less hassle. If you want to avail our service, call us now and get a metal forgings quote!