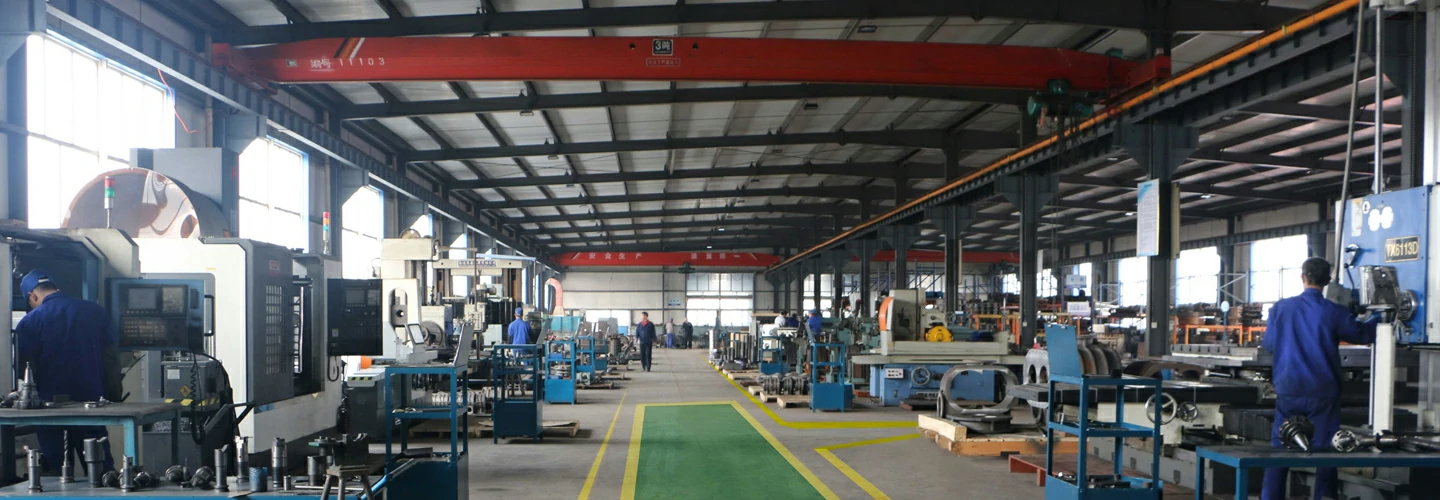
China Cnc Machining Service After Forging
Cnc Machining Forgings is the process of removing excess material and achieving exact dimensions as per the requirements. The process of cnc machining converts the metal forged part into a fully finished and ready-to assemble component.Pintejin provides a variety of precision CNC machining services For Metal forgings. With precision 3-, 4- and 5-axis CNC machining centers, combined with other advanced capabilities and our experienced team, we can handle all types of CNC machining parts in both forging parts.Here our machining service can be seperated into two parts, one is Rough Machining, and the other is Precison Machining.
- Rough machining mainly means some simple machining works done by machining equipments like drilling machine, milling machine, nc lathes, and some other small machining equipments.
- For more accurate tolerances, precision machining will be required by CNC, which will charge you high machining cost for the high equipment cost and labour cost. So our in-house machining service includes: turning, milling, roll threading, cut threading, grinding, and die manufacturing.
The Design Basis Of Cnc Machining Forgings
The Positioning Datum Of Cnc Machining Forgings
- a. Automatic centering positioning: such as three-jaw chuck positioning.
- b. Positioning sleeve positioning: the positioning element is made into a positioning sleeve, such as the positioning of the stop plate
- c. Others include positioning in the V-shaped frame, positioning in the semi-circular hole, etc.
The Measurement Datum Of Cnc Machining Forgings
The Assembly Datum Of Cnc Machining Forgings
The Advantage Of Cnc Machining Forgings
- Improve the internal structure and mechanical properties of forgings. After the forging process, the structure and properties of the forging blank are improved and improved. The forging process can eliminate the defects such as pores, shrinkage holes and dendrites inside the metal ingot, and due to the plastic deformation and recrystallization of the metal, it can make coarse The grain is refined to obtain a dense metal structure, thereby improving the mechanical properties of the forging. In the design of parts, if the force direction and fiber structure direction of the parts are correctly selected, the impact resistance of the parts can be improved.
- The utilization rate of materials is high. Metal plastic forming is mainly based on the relative position rearrangement of the shape and structure of the metal, without the need to remove the metal.
- Higher productivity. Forging processing is generally performed using a press and a forging hammer.
- The precision of the blank or forging is higher. Shanxi Yongxinsheng Forging applies advanced technology and equipment to achieve less or no cutting.
- The metal material used for forging should have good plasticity, so that under the action of external force, it can produce plastic deformation without breaking. Among the commonly used metal materials, cast iron is a brittle material with poor plasticity and cannot be used for forging. Copper, aluminum and their alloys in steel and non-ferrous metals can be press worked in cold or hot state.
- It is not suitable for forgings with complex shapes. Forging is formed in a solid state. Compared with casting, the flow of metal is limited, and generally requires process measures such as heating to achieve. It is difficult to manufacture parts or blanks with complex shapes, especially with complex inner cavities.
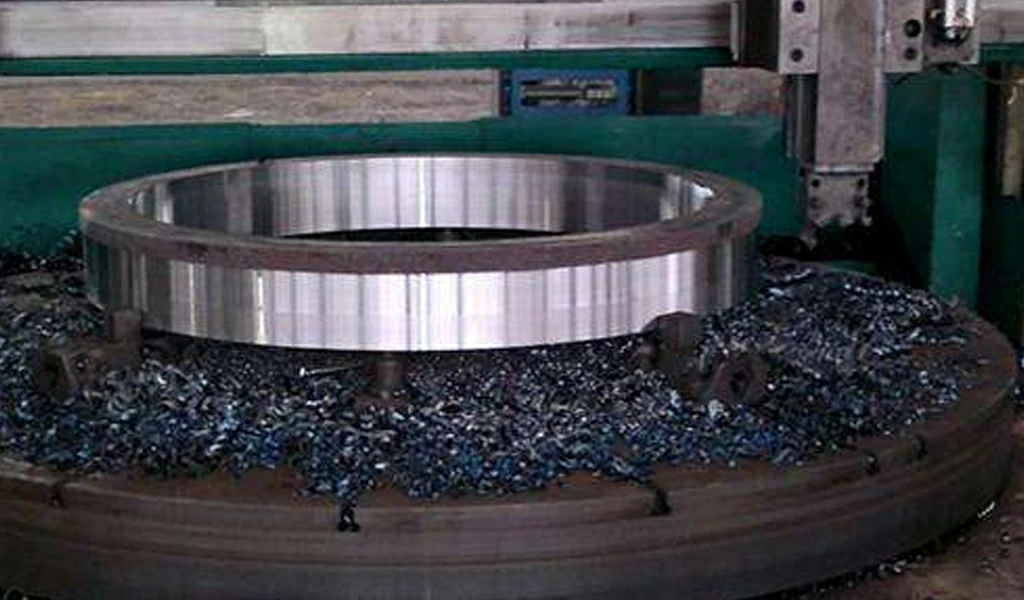
The Division Of Forgings In The Cnc Machining Stage
When the surface precision and roughness requirements of forgings are relatively high, it often needs multiple cnc machining to complete. In order to ensure the cnc machining quality, the entire process should be divided into several cnc machining stages.
The 4 Cnc Machining Stages Of The Process
It should be pointed out that the division of processing stages refers to the entire process of forging processing, and cannot be judged by the processing of a certain surface or the nature of a certain process. At the same time, in specific applications, it cannot be absolute. For some heavy parts or forgings with small margins and low precision, the roughing and finishing of the surface can be completed after one clamping.
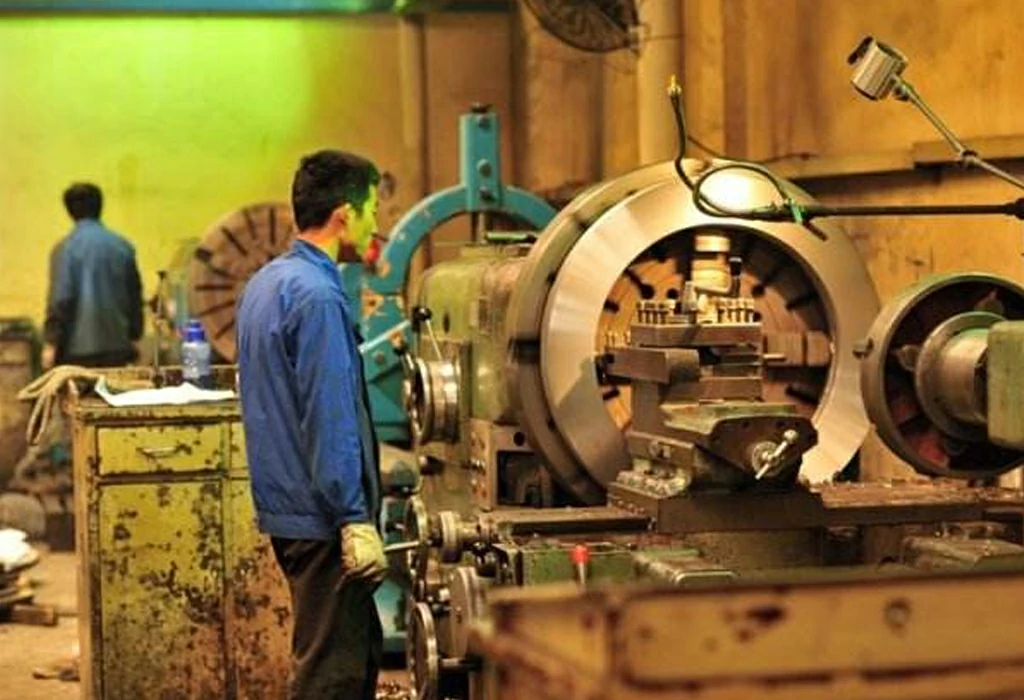
- Roughing stage. Most of the machining allowance on each surface is mainly removed, so that the shape and size of the blank are close to the finished product. The characteristics of this stage are the use of high-power machine tools, the selection of larger cutting amounts, the improvement of productivity and the reduction of tool wear as much as possible.
- Semi-finishing stage. Finishes the secondary surface and prepares the primary surface for finishing.
- Finishing stage. Ensure that the main surface meets the drawing requirements.
- Finishing stage. For the surface with high surface roughness and processing accuracy, finishing processing is also required. This stage generally cannot be used to improve the positional accuracy of forgings.
The Reasons For Dividing Cnc Machining Stages
When drawing up the process route of forgings, the principle of dividing the cnc machining stages should generally be followed, but the specific application should be handled flexibly. For example, for some refined blanks, parts with low machining accuracy and high rigidity need not be divided into machining stages. For another example, for some heavy forgings with good rigidity, due to the difficulty of hoisting, they often do not divide the cnc machining stage and complete the roughing and finishing after one clamping.The division of cnc machining stages is for the entire cnc machining process of the part, and cannot be judged from the cnc machining of a certain surface or the nature of a certain process.
For example, the finishing of some positioning base surfaces should be completed in the semi-finishing or even roughing stage and cannot be placed in the finishing stage.
- It is beneficial to ensure the cnc machining quality. After rough machining of forgings, due to the large machining allowance, the cutting force and clamping force are also large, which will cause large deformation and stress redistribution. , will affect the machining accuracy; and after dividing the machining stage, the deformation can be gradually restored and corrected, and the machining quality can be improved.
- It is convenient to use the equipment reasonably. Rough machining requires machine tools with good rigidity, high efficiency and low precision, while finishing requires high machine tool accuracy. After dividing the cnc machining stage, it is possible to avoid being lean and rough, give full play to the performance of the machine tool, and prolong the service life of the machine tool.
- It is convenient to arrange the heat treatment process and the inspection process. After the roughing stage, a stress-relieving heat treatment is generally arranged to relieve stress. Some parts require final heat treatment such as quenching before finishing, and their deformation can be eliminated by finishing.
- It is convenient to find defects in time and avoid damage to the processed surface. After rough machining, the defects are exposed, which can be found and dealt with in time. At the same time, the finishing process is placed at the end, which can prevent the machined surface from being damaged during handling and clamping.
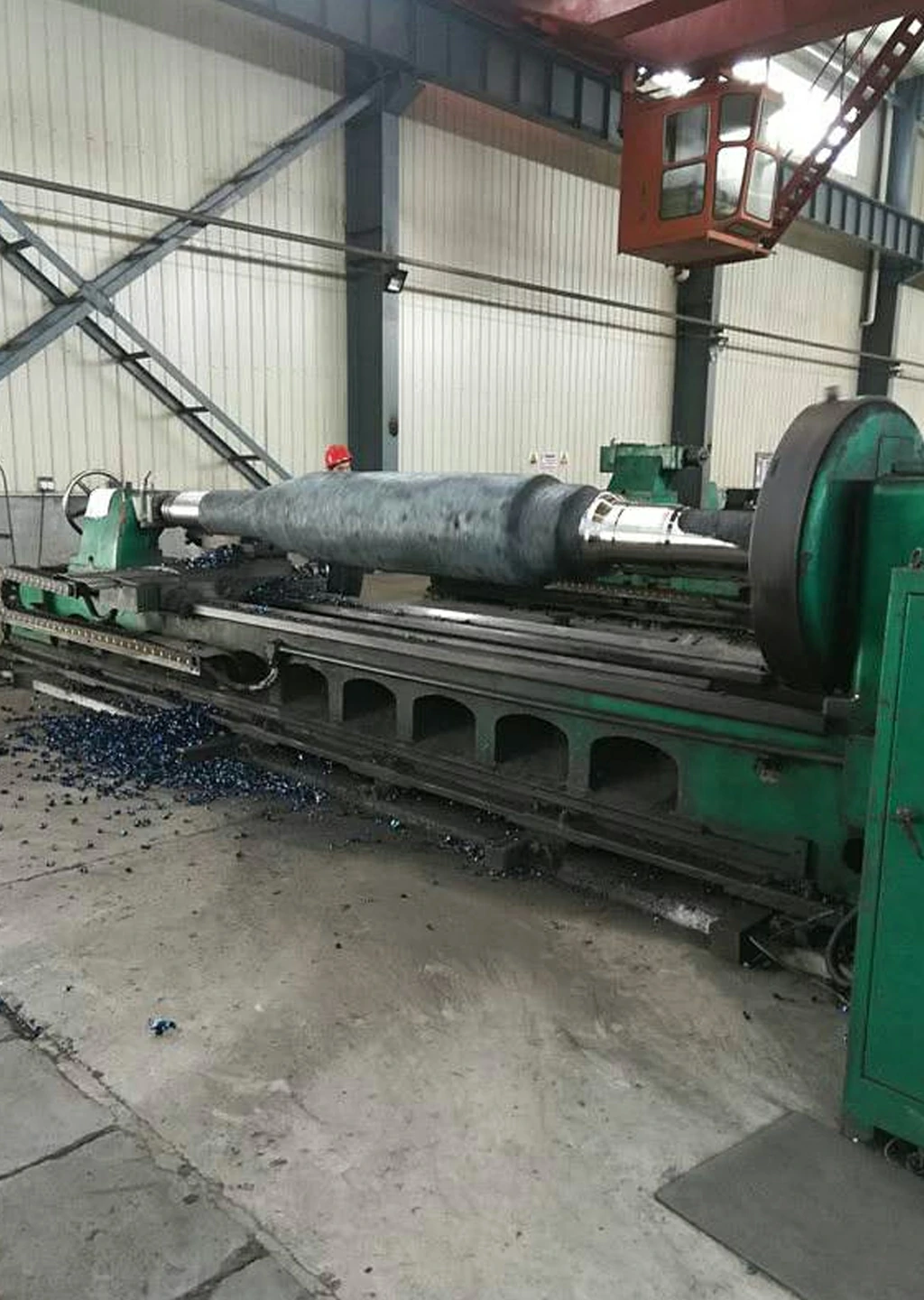
NEED NOT TO LOOK FURTHER BECAUSE Pintejin IS HERE TO HELPLooking For CNC Machining Services Make Your Work Less Hassle.Pintejin Group is a CNC machining specialist that can help you choose a machinable metal for your next project. Contact us for a free quote.