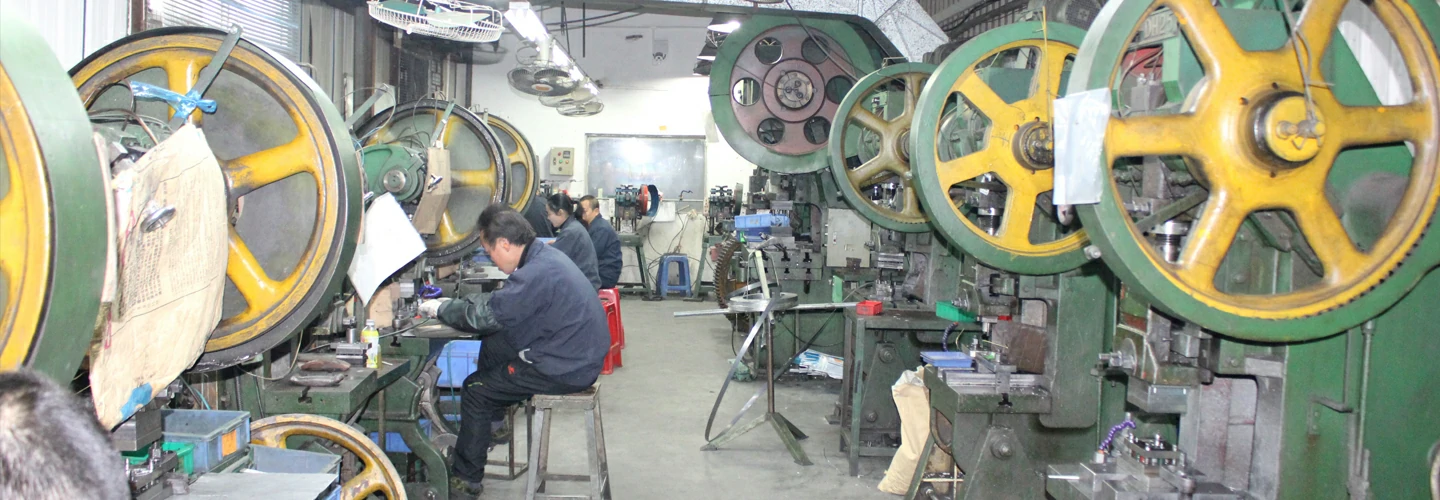
Cold Forging Parts Factory In China
A general term for plastic processing such as cold die forging, cold extrusion, and cold heading. Cold forging is the forming process of the material below the recrystallization temperature, and the forging is carried out below the recovery temperature. In production, forging without heating the blank is called cold forging. Most of the cold forging materials are aluminum and some alloys, copper and some alloys, low carbon steel, medium carbon steel, and low alloy structural steel with low deformation resistance and good plasticity at room temperature. Cold forgings have good surface quality and high dimensional accuracy, which can replace some cutting processes. Cold forging can strengthen the metal and increase the strength of the part.Cold Forging encompasses many processes like bending, cold drawing, cold heading, coining, extrusions and more, to yield a diverse range of part shapes. The temperature of metals being cold forged may range from room temperature to several hundred degrees.
The fast hydraulic press is the main cold forging equipment of Pintejin Company. At present, the company has a cold forging production line with 650 tons of four-column rapid hydraulic press, 200 tons of cold forging rapid hydraulic press, and 160 tons of rapid cold extrusion press as the main machine. After 2020, it will increase by 1000 tons and 1,600 tons of cold forging presses, with an annual design capacity of 8,000 tons.
Pintejin has complete cold extrusion, and cold forging die design, manufacturing, and a full range of product development and manufacturing capabilities. The production line can adopt multi-station cold precision forging,and other high-quality forgings, totaling thousands of types and weighing 5 kg,The precision level can reach the international advanced standard of cold precision forging. It can carry out cross-series metal parts supporting cooperation according to customer and project overall/strategic procurement requirements. This includes hot forging, warm forging, machining, and heat treatment.
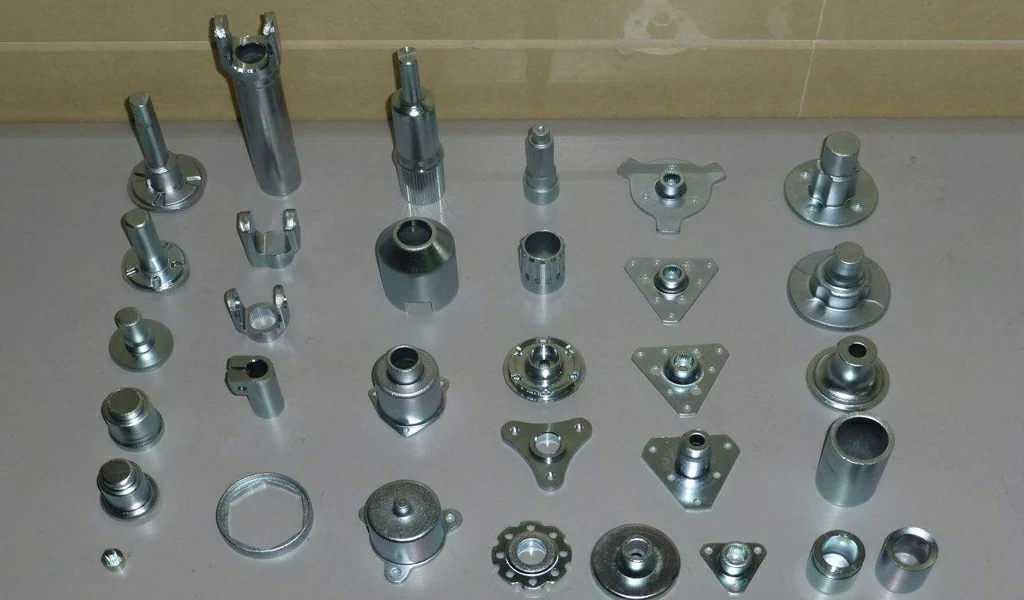
What Is Cold Forging
Cold forging, also known as cold volume forming, is a manufacturing process and a processing method. It is basically the same as the cold stamping process. The cold forging process is also composed of three elements: material, mold and equipment. It’s just that the materials in stamping are mainly plates, while those in cold forging are mainly discs or wires.
In Japan, it is called cold forging (cold forging for short), in China it is called cold heading, and some screw factories also like to call it head.
Cold Forging Define
Cold forging refers to various volume forming performed below the recrystallization temperature of the metal. It can be known from the theory of metallography that the recrystallization temperature of various metal materials is different; T re=(0.3~0.5) T melting. T melting is shown in the table below:
Metal | Minimum Recrystallization Temperature /℃ |
---|---|
Iron (Fe) and Copper | 360~450 |
Tin (Sn) | 0 |
Copper (Cu) | 200~270 |
Lead (Pb) | 0 |
Aluminum (Al) | 100~150 |
Tungsten (W) | 1200 |
It can be known from the figures in the table: the minimum recrystallization temperature of iron metal and non-metal. Even at room temperature or room temperature, the forming of lead and tin cannot be called cold forging, but hot forging. However, iron, copper, and aluminum can be called cold forging when they are formed at room temperature.
The shape of cold forged parts is becoming more and more complex, from the initial stepped shaft, screw, nut and conduit, etc., to parts with complex shapes.
The typical process of spline shaft is: positive extrusion rod part – upsetting middle head part – extrusion spline;
The main process of the spline sleeve is: reverse extrusion of the cup-shaped part – punching the bottom to make a ring part – positive extrusion of the shaft sleeve.
The cold extrusion technology of cylindrical gears is also successfully used in production. In addition to ferrous metals, cold extrusion applications of copper alloys, magnesium alloys and aluminum alloys are also becoming more and more extensive.
The Application Scope Of Cold Forging
Precision Cold Forging
Cold precision forging is a (near) net shape forming process. The parts formed by this method have high strength and precision and good surface quality. At present, the total amount of cold forgings used in an ordinary car abroad is 40~45kg, of which the total amount of toothed parts is more than 10kg. The single-piece weight of cold forged gears can reach more than 1kg, and the tooth shape accuracy can reach 7 grades.
Continuous process innovation has promoted the development of cold extrusion technology. Since the 1980s, domestic and foreign precision forging experts have begun to apply the split forging theory to the cold forging of spur and helical gears. The main principle of shunt forging is to establish a shunt cavity or shunt channel of material in the forming part of the blank or die. During the forging process, while the material fills the cavity, part of the material flows to the shunt cavity or shunt channel. The application of shunt forging technology enables the less and no cutting processing of higher precision gears to quickly reach an industrial scale. For extruded parts with a length-diameter ratio of 5, such as piston pins, cold extrusion can be achieved at one time by axial shunt by using a wide range of axial residual blocks, and the stability of the punch is very good; for flat spur gears Forming, the use of radial residual blocks can also achieve cold extrusion forming of products.
Blocked forging is to extrude metal in one or two directions through one or two punches in a closed die at one time to obtain near-net shape precision forgings without flash. If some car precision parts such as planetary and half shaft gears, star sleeves, cross bearings, etc. are processed by cutting, not only the material utilization rate is very low (less than 40% on average), but also it takes a lot of man-hours and the production cost is extremely high. These net shape forgings are produced in foreign countries using occlusion forging technology, which saves most of the cutting process and greatly reduces the cost.
The Skills Requirement Of Precision Cold Forging
The forming accuracy of cold forging technology is higher than that of warm forging and hot forging, and it has its unique advantages in the field of precision forming. The application of the cold forging process improves the bore finish, dimensional accuracy and surface strength, prolongs the life of the barrel, and improves the shooting accuracy of the gun accordingly, and it is easy to process the tapered barrel and reduce the quality. The cold forging process was first proposed by Steyr, and later many countries in the world adopted the cold forging machine of Steyr to process the barrel.
The Technological Development Of Cold Forging
The development of cold forging technology is mainly to develop high value-added products and reduce production costs. The combination of processes constitutes a composite process. Hot forging-cold forging composite plastic forming technology is a new precision metal forming process that combines hot forging and cold forging. Therefore, the main deformation process is completed by hot forging; the precision of cold forgings is high, so the important dimensions of the parts are finally formed by the cold forging process. The hot forging-cold forging composite plastic forming technology appeared in the 1980s, and has been widely used since the 1990s. The parts manufactured by this technology have achieved good results in improving precision and reducing costs.
Numerical Simulation Technology
Numerical simulation technology is used to verify the rationality of the process and mold design.
With the rapid development of computer technology and the development of the plastic finite element theory in the 1970s, many problems that are difficult to solve in the plastic forming process can be solved by the finite element method. In the field of cold forging forming process, through modeling and the determination of appropriate boundary conditions, finite element numerical simulation technology can intuitively obtain the stress, strain, die force, die failure and possible defects in the metal flow process. . The acquisition of these important information has important guiding significance for the rational mold structure, mold material selection, heat treatment and final determination of the forming process plan.
Effective numerical simulation software is established on the basis of rigid-plastic finite element method, such as Deform, Qform, Forge, MSC/Superform and so on. The use of finite element numerical simulation technology can be used to test the rationality of process and mold design. The pre-forging split zone-split final forging was numerically simulated with the three-dimensional finite element numerical simulation software Deform 3DTM, and the forging load-stroke curve and the stress, strain and velocity distribution of the entire forming process were obtained, which were compared with the traditional closed-type numerical simulation software. The results of the upsetting extrusion process simulations are compared. The analysis shows that the traditional closed upsetting and extruding spur gear has a large forming load, which is not conducive to the filling of the tooth shape. The new process of pre-forging split area-split final forging can greatly reduce the forming load, significantly improve the filling property of the material, and obtain gears with full tooth corners. The numerical simulation of gear cold precision forging process is carried out by three-dimensional large deformation elastic-plastic finite element method. The deformation flow situation was analyzed numerically. Numerical analysis results and process tests show that the diversion in final forging, especially the diversion measures of restricted holes, is very effective in reducing the working load and improving the filling capacity of corners.
Intelligent Design Technology
Intelligent design technology and its application in cold forging forming process and die design.
The Columbus Betel Laboratory in the United States has developed a knowledge-based pre-forging geometry design system. Because the shape of the pre-forging is designed as a spatial geometry, the geometry must be manipulated, so the reasoning process cannot be described simply by general language. For the geometric information of the part, the frame method is used to represent, in the frame, different slots are used to define the basic components and the topological relationship between them. Design rules are expressed by production rules and manipulated with OPS tools.
The application of knowledge-based design method in cold forging forming process and die design will completely change the traditional state of plastic forming that relies on the experience of all designers, repeated revisions in the design process, and low design efficiency. It uses artificial intelligence, pattern recognition, machine learning and other technologies to extract appropriate knowledge from the system knowledge base during the design process to guide the cold forging forming process and die design. The technology is under further development. The knowledge-based design method has become a characteristic subject in the research of forging forming process and intelligent technology of die design.
The Advantages And Disadvantage Of Cold Forging
The Advantages Of Cold Forging Process
The cold forging process is a precision plastic forming technology with unparalleled advantages in machining, such as good mechanical properties, high productivity and high material utilization, especially suitable for mass production, and can be used as a manufacturing method for final products. (Net-shape Forming), which has a wide range of applications in industries such as transportation, aerospace and machine tool industries.
The Disadvantages Of Cold Forging Process
High material requirements; not suitable for small amount processing; high mold requirements
Provide Cold Forging Service To Make Your Work Fast & Easy
Pintejin focuses on product development and cold forging manufacturing of metal parts and components. Compared with other technologies such as turning, engraving or hot forging, our cold forging products have a good surface finish and are close to the net shape. There is almost no need for finishing, which saves manufacturing costs. The cold forging processing technology is particularly suitable for the long-term production of lightweight parts.
The products that can be produced by cold forging processing technology are screws, fasteners, nuts, bolts, suspension parts, anti-locking systems, shafts, bits, clutch hubs, gears, pinions, pins, threads, transmission gears, intermediate shafts, Shaft sleeves and so on.
Common raw materials used for cold forging mainly include carbon steel, alloy steel, stainless steel, aluminum alloy, and copper alloy. Commonly used are Al6061, Al7075, 45#, Q235, Q345, 35Mn, 65Mn, 40Cr, 35CrMo, 42CrMo, 4140, 20CrMnTi, 20CrNiMo, 304, 310, 316, 431, Al, Copper, etc.
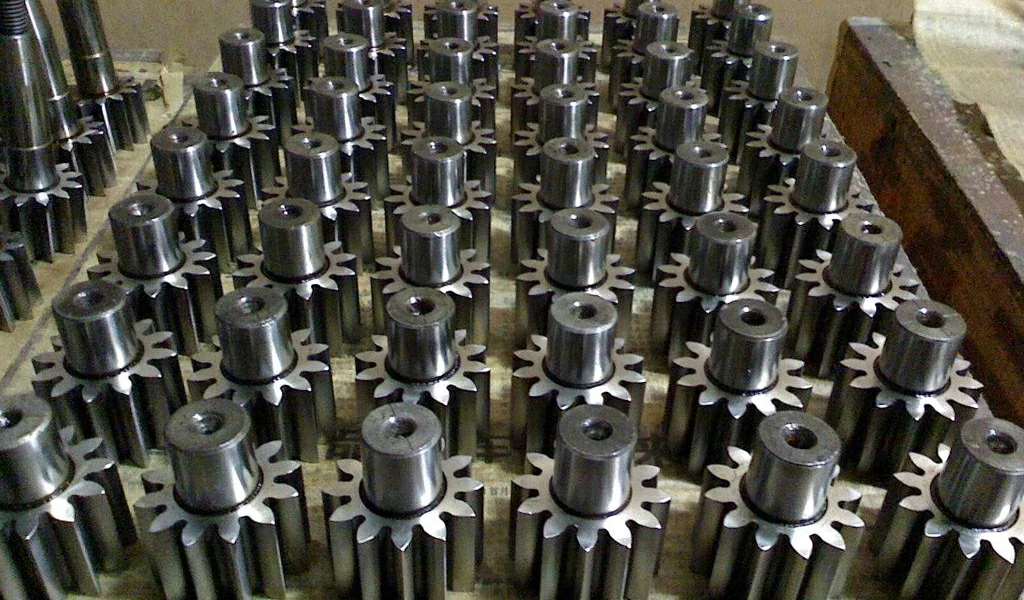
Cold Forging Part In China Cold Forgings Suppliers
As a professional forging manufacturer, Pintejin has extensive forging expertise, such as hot forging, warm forging and cold forging, as well as design and engineering expertise. With our unparalleled manufacturing capabilities, we strive to challenge long-term practices to constantly exceed the established framework constantly.We have many years of experience in manufacturing a variety of high-performance, critical and safety components.
-
Forging 5083 5052 6061 7075 2A12 Aluminum Flange
-
Aluminum Alloy Forged Mountain Bike Shoulder Cover
-
Aluminum Hot Die Forging Automotive Parts
-
Aluminum Alloy Die Forged Bike Folder Shoulder Cover V Brake Parts
-
Aluminum Alloy Hot Forged Bike Transmission Hook
-
Die Forged Packing Belt Connecting Mesh Ring
-
Forged Carbon Steel Special-Shaped Split Flange
-
Custom Forged Special-Shaped Hinge Spade Pins
If you are looking for Metal Forging Service,Pintejin is ready to give them to you! With us, you will have the opportunity to make your custom Hot forging parts, cold forging parts,machined parts, prototype production easy and less hassle. If you want to avail our service, call us now and get a metal forgings quote!