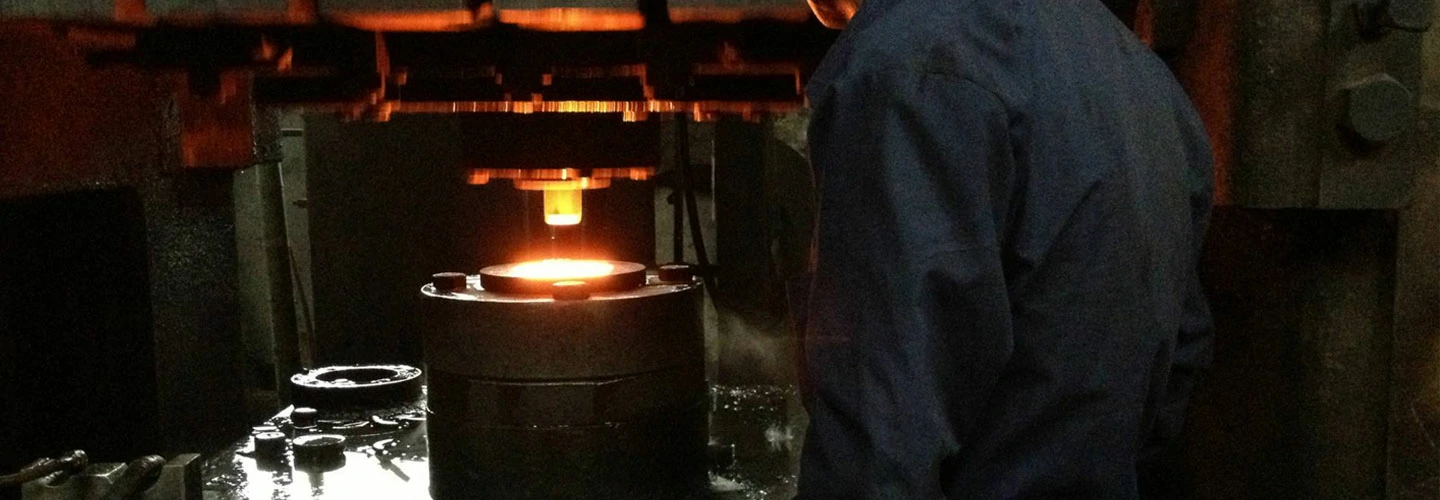
Martensitic Stainless Steel Forging
Martensitic stainless steel has high hardenability, which can be hardened by air cooling. Therefore, when cold forging martensitic steels, especially those high carbon steels, protective measures must be taken to prevent the occurrence of cracking. Generally, martensitic steel should be covered with heat insulating material, or evenly cooled in the furnace to cool it slowly to 593℃. If the forging is directly cooled by water jet like cooling the forging die, it will cause forging cracking.
Generally, martensitic stainless steel forgings are tempered after forging to reduce the hardness of the steel so that it can be machined. After machining it is fire-hardened and then tempered.
The maximum forging temperature of martensitic stainless steel should be selected below the temperature produced, otherwise cracks will easily occur. Usually formed at a temperature of 1093~1260°C. Special care must be taken not to exceed this temperature during forging and to avoid localized overheating due to rapid metal movement. In addition, surface decarburization will promote the formation of ferrite, so it should be limited.
As the chromium content increases, the formation temperature of ferrite decreases, while a small amount of ferrite significantly reduces its forgeability. When the ferrite is increased to more than 15%, the forgeability will gradually increase again until the structure completely becomes ferrite. The final forging temperature is limited by the allotropic transformation (the isomorphic transformation starts at around 816°C), and this steel is usually stopped at 927°C, because it is difficult to form if the temperature is too low.
Adding sulfur or smashing to Y12Crl3 (416) steel can improve its machinability, but these elements can also cause forging problems, especially when they form a surface plate-like structure, it is easy to produce cracks. However, it can be eliminated by adjusting the forging temperature and process method. If sulfur is added, it is impossible to eliminate this kind of cracking. From this point of view, adding selenium is better.
Martensitic stainless steel should avoid the formation of S-ferrite during forging and heating, because the appearance of ferrite will cause cracks in the forging. It is necessary to avoid overheating of stainless steel forgings caused by heating too fast. The decarburization of the forging during the heating process is mainly to promote the formation of ferrite, so the decarburization of the forging surface should be minimized. There is no special requirement for the deformation amount of martensitic stainless steel in the last fire. This kind of steel is prone to cracking after forging. The reason is that martensite and carbide structures appear during air cooling after forging, and the internal stress is large. Therefore, cooling after forging must be carried out slowly, generally at 200 ℃ sand pit or Slow cooling in the slag, isothermal annealing must be carried out in time after taking out the sand pit to prevent cracking.
Martensitic stainless steels, especially Crl3 martensitic stainless steels have low prices, so they are widely used in less corrosive media (such as water vapor) and require high mechanical properties. 12Crl3 steel is semi-martensitic stainless steel, in addition to martensitic structure, there is also ferrite structure in the steel.
The Characteristics Of Martensitic Stainless Steel Forging
- Martensitic (20Crl3, 40Crl3, 14Crl7N12, etc.) stainless steel undergoes allotropic transformation in the process of heating and cooling. For this type of steel, there is no special requirement for the final-fire deformation.
- The formation of 8-ferrite should be avoided during forging and heating of martensitic stainless steel, because the appearance of ferrite will cause cracks in the forging, and it is necessary to avoid overheating caused by excessive heating of the metal. Surface decarburization of forgings can cause excessive ferrite formation, so surface decarburization should be minimized.
- Martensitic stainless steel is prone to cracking after forging. This is because martensite and carbide structures will appear during air cooling after forging, and the resulting internal stress is large, so it should be cooled slowly after forging. Slow cooling in the pit or slag, and annealing should be carried out in time after being taken out from the sand pit to prevent breakage.
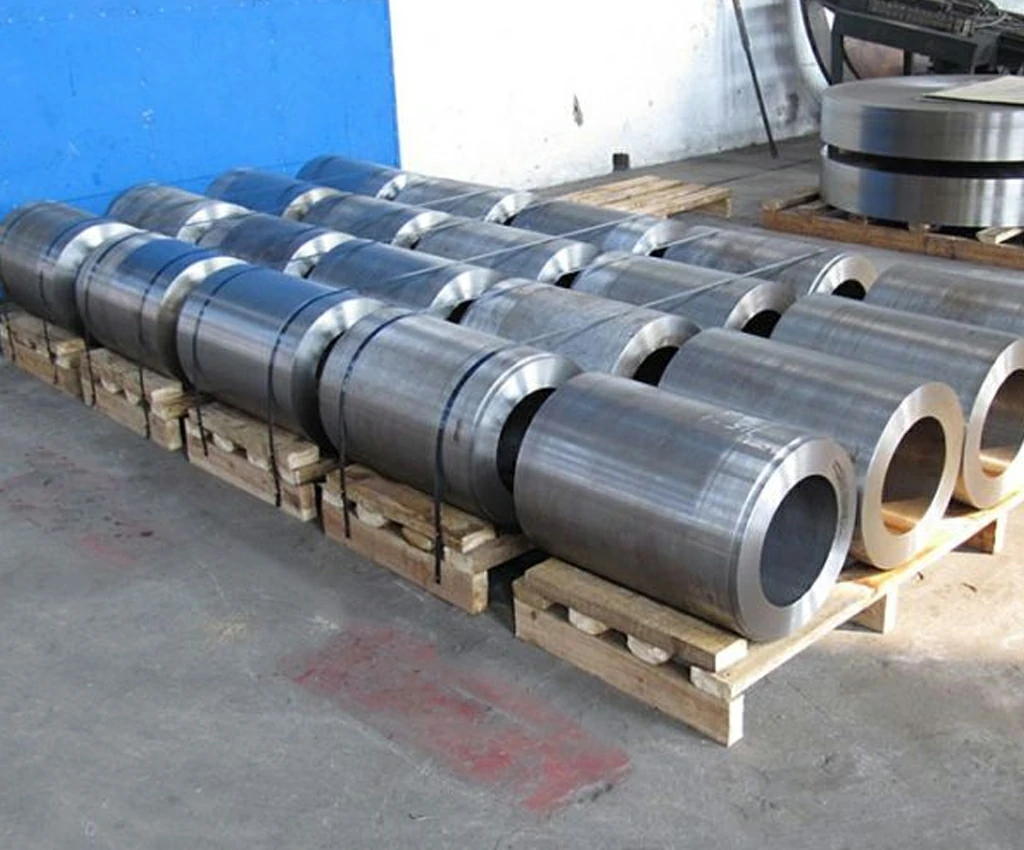
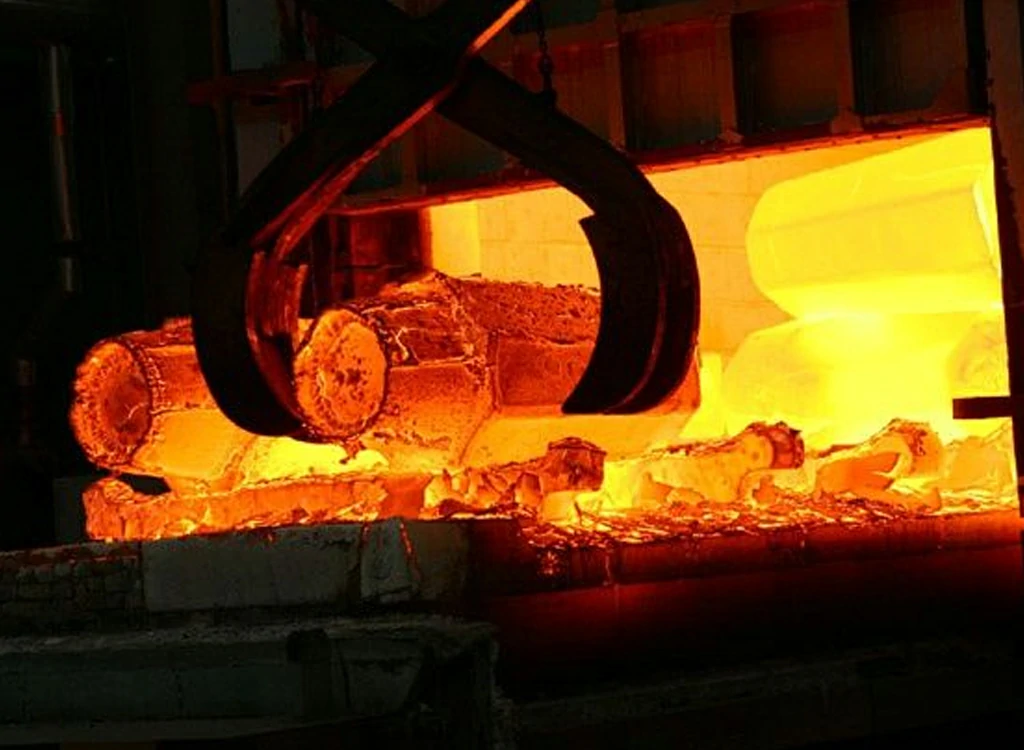
Martensitic Stainless Steel Forging Temperature Range
The initial forging temperature of martensitic stainless steel is affected by the high temperature ferrite formation temperature and the ferrite state.
The initial forging temperature of martensitic stainless steel is generally 1150 °C. The final forging temperature varies with the carbon content. When the carbon content is high, it is generally 925 °C, and when the carbon content is low, it is generally 850 °C, which should be higher than the same temperature of the steel. Primitive isomerization transition temperature.
With custom-machined dies and a cost-effective forging process that reduces post-processing, Our forging company strives to produce products that not only last longer but are engineered for maximum strength and quality. Contact us today for more details.