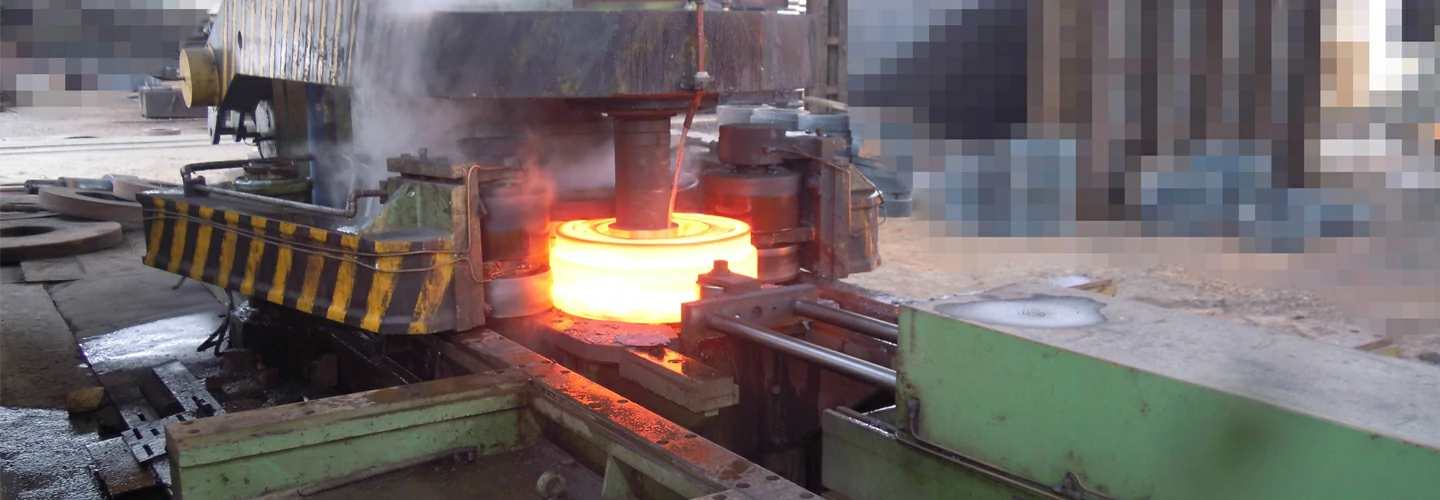
Roll Forging – Ring Forging
Roll forging is a type of rotary forging. Roll Forging(Ring forging) is a processing method that plastically deforms the billet or ingot under the action of ring equipment and tools (die) to obtain a forging of a certain ring size.This is the introduction of longitudinal rolling into the forging industry in recent decades and the continuous development of a new forging process, which belongs to the category of rotary compression forming.Roll forging is a plastic forming process in which the material is plastically deformed under the action of a pair of counter-rotating dies to obtain the desired forging or forging blank. It is a special form of forming rolling (longitudinal rolling).
Custom manufacturer of forgings for aerospace, automotive, defense, hydraulics, oil, gas, marine and military industries. Available in +/- 0.01 mm tolerance. Coin presses, roll, rotary, upset, cored, drop, extrusion press, flat die, hammered, hand, near net shape and infrared forging methods are provided. Made from aluminum, brass, bronze, copper, Invar®, iron, magnesium, steel, titanium, ferrous and non-ferrous metals. We keep an inventory of mandrel rolled ring metal forgings with a diameter up to a maximum of 70” and 16” minimum ID. They come in a maximum length of 65” up to 25,000 pounds.Suitable for blades, flanges, gears, shafts, tools, valves, wheels and other products. Prototype and low to high volume production is available.At Pintejin, our experience and dedication to superior services allow us to help you find the best custom roll forgings service for your needs. With over 30 years of experience in forging, we know what it takes to create high-quality and precise roll forging parts.
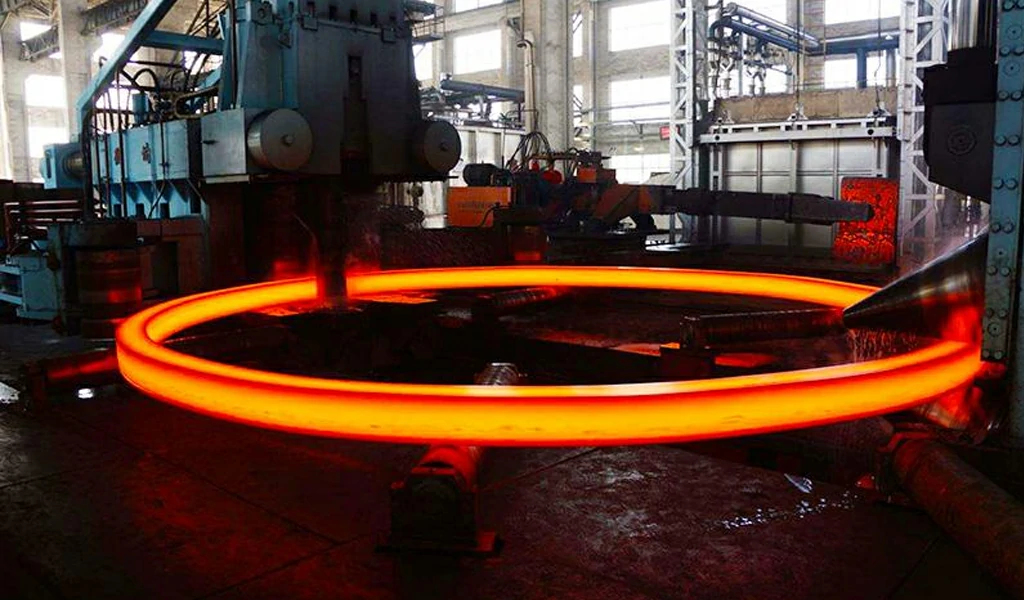
The Classification Of Roll Forging
Roll forging is divided into billet roll forging and forming roll forging. Billet roll forging is to prepare blanks of required shape and size for die forging; forming roll forging can directly produce forgings that meet the shape and size requirements.
The essence of roll forging deformation is the rolling extension of the billet, and the section of the billet part becomes smaller and the surface area increases. When the deformation of the section is large, it needs to be rolled for several times. The process design is mainly to reasonably determine the reduction amount, the expansion amount and the extension deformation amount of each step of the roll forging. They depend on the size of the roll diameter, the shape and size of the hole, the temperature of the blank and the deformation conditions such as cooling and lubrication. One end of the blank is clamped with clamps, deformed under the rolling of the first pass of the fan-shaped die (initial forming) and withdrawn; ) and exit; according to the needs of deformation, it is gradually formed by multiple rollers to obtain the desired formed workpiece (final forming). It is the most commonly used reverse roll forging method. When the feeding direction is along the rotation direction of the roller, it is called forward rolling, and the clamp is released immediately after the workpiece is bitten. The most commonly used roll forging machine is a double-supported roll forging machine with frame support on both sides. It has greater rigidity and can obtain high-precision forgings. Its roll diameter has a variety of specifications from 250 to 1250 mm. The forging force is 400 to 4000 kN. Some double-support roll forging machines have roll shafts protruding from one end. This is a composite roll forging machine that combines cantilever type and double-support type. It can realize both longitudinal roll forging and lateral widening at the cantilever end. In mass roll forging production, manipulators are widely used to transfer workpieces to automate the production process, improve productivity and reduce labor intensity.
The Deformation Characteristics Of Roll Forging
The Fundamental Of Roll Forging
(1) The biting of the billet The roll forging process can be established only when the billet is bitten by the roll forging die. Naturally bite into the end, the friction between the mold and the blank is the main driving force for bite, and the component force of the pressure p on the blank is the resistance to bite, and α is called the bite angle. Increasing the friction coefficient and reducing the bite angle is beneficial to realize the bite condition. The increase of the friction coefficient can be achieved by roughening the surface of the mold, and the reduction of the bite angle can be achieved by reducing the absolute reduction. The middle bite is that the protruding part on the roll forging die directly presses the billet and forcibly pulls the billet into the deformation zone. The bite is not affected by friction and the bite angle can be increased. In order to reduce the number of roll forging passes, it is necessary to increase the reduction amount per pass and use intermediate bites. The bite angle is not more than 25º when the end is naturally bitten, and can reach: 32º~37º when the middle bit is bitten.
(2) In the process of front sliding roll forging, the volume of material flowing into the deformation zone and flowing out of the deformation zone at each moment is equal, and the height of the deformation zone changes, so the moving speed of the material along the roll forging direction also changes, at the exit of the deformation zone The moving speed of the material is greater than the linear speed of the forging roll. This phenomenon is called forward slip. Since the length of the roll forging is determined by the moving speed at the exit, it is of great significance to calculate the forward slip. The Funk formula for calculating the forward slip is:
S=(R/h-1/2)r2
r=(α/2)×(1-α/2β)
- where S is the forward slip value;
- R——roll forging die radius;
- α – bite angle;
- β – friction angle;
- h——The height at the exit of the deformation zone.
Fink’s formula is derived under the condition of ignoring Kuanmin, and it is an approximate formula for calculating simple deformation. For the longitudinal variable section roll forging constrained by the groove, the forward slip value is smaller than that of the simple roll forging.
(3) The widening material flows in the lateral direction through roll forging to form a widening. The main factors affecting the widening are: the absolute reduction, the diameter of the roll forging die, the original width of the billet and the friction coefficient. The increase in absolute reduction, the increase in the diameter of the roll forging die, the increase in the friction coefficient, and the decrease in the width of the original blank all increase the spread. Theoretically, there are many formulas for calculating the widening, but they are all proposed under a certain condition, and the error is large when calculating the complex groove roll forging. At present, the corresponding rectangle method is adopted, that is, the groove is converted into a rectangle, and the formula for flat roll rolling is borrowed, and then corrected.
The Mould Design Points Of Roll Forging
- For billet roll forging, the billet should be selected according to the requirements of calculating the billet diagram, the roll forging pass should be calculated according to the maximum deformation degree, the groove system should be selected, and the deformation amount of the pass should be allocated reasonably. According to the deformation law, the section size of the billet for each pass is calculated, so that the deformation of each pass can be adapted, and the rational selection of the groove system is the key. Groove scheme, Table 2 lists common grooves. When selecting the groove system, in addition to the reasonable distribution of the deformation, the stability of the roll forging should be considered. Pay attention to the matching relationship between the shape of the groove and the blank, and also consider that the increase in deformation is limited by the stability conditions.
- For forming roll forging grooves, in addition to the main points of roll forging design, the requirements for formability and dimensional accuracy should also be considered. During roll forging, the rear slip area occupies most of the deformation area, so the rear wall of the groove is easy to form while the front wall is difficult to form. By changing the rolling direction, the front and rear walls can be placed in an easy forming area, so that the groove is well filled. Accurate calculation of the forward slip value can ensure the dimensional accuracy in the length direction. In addition to theoretical calculations, it is also important to refer to examples of existing measured data.
The Equipment Of Roll Forging
The Material Of Roll Forging
- AISI 1010, AISI 1018, AISI 1020, AISI 1026, AISI 4130, AISI 4140, AISI 4330, AISI 4340, AISI 8620, AISI 8630, AISI 9310, Nitralloy 135
- Stainless Steel 300 Series
- Grade 302, Grade 304, Grade 304-l, Grade 309, Grade 310, Grade 316, Grade 316-L, Grade 317, Grade 321, Grade 330
- Stainless Steel 400 Series
- Grade 403, Grade 405, Grade 410, Grade 414, Grade 416, Grade 418, Grade 422, Grade 431, Grade 440-A, Grade 440-C
- Precipitation Hardening Grades
- 13-8MO, 15-5 PH, 17-4 PH, 450, 455
- Duplex stainless-steel grades: 2205, 2507, F-55
- Monel: 400, K 500
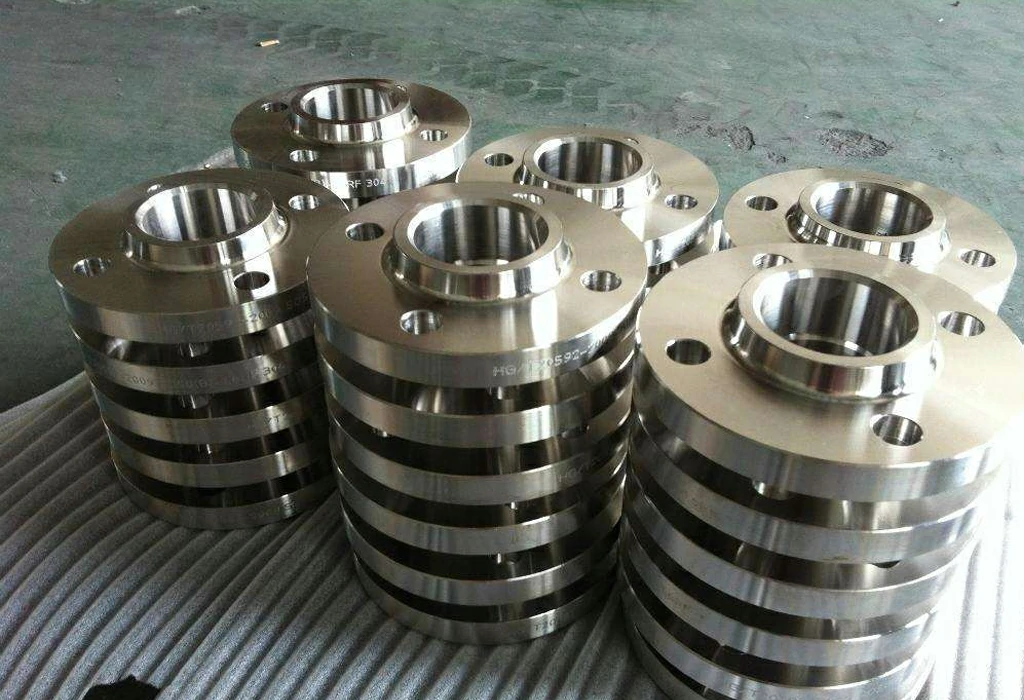
What Is Roll Forging – Roll Forging Define
Roll forged are metal products process shaped by a series of rollers, during the process known as roll forming.Roll forging has higher technical and economic advantages than die forging. It is characterized by less required working load, high production efficiency, less material consumption, superior quality and good working conditions.
The principle of roll forging deformation is shown in Figure 1. Roll forging deformation is a complex three-dimensional deformation. Most of the deformed material flows along the length direction to increase the length of the blank, and a small amount of material flows laterally to increase the width of the blank. During the roll forging process, the cross-sectional area of the billet is continuously reduced. Roll forging is suitable for deformation processes such as shaft drawing, slab rolling and material distribution along the length direction.
Roll forging can be used to produce connecting rods, twist drills, wrenches, spikes, hoes, picks and turbine blades. The roll forging process uses the rolling forming principle to gradually deform the blank. Compared with ordinary die forging, it has the advantages of simpler equipment structure, stable production, low vibration and noise, easy automation and high production efficiency.
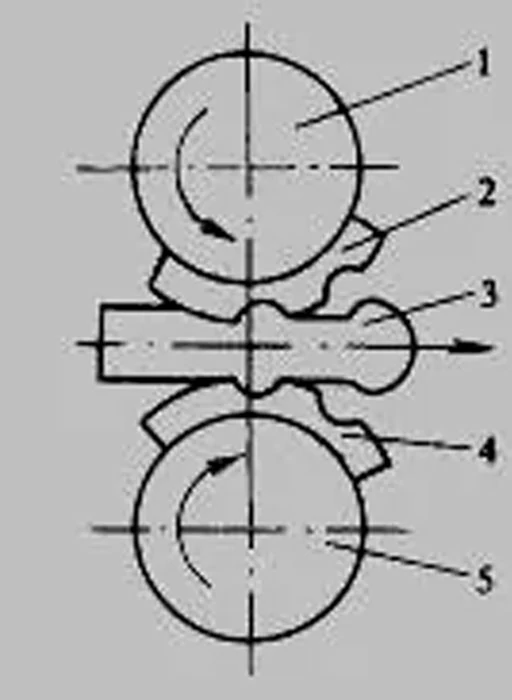
With custom-machined dies and a cost-effective forging process that reduces post-processing, Our forging company strives to produce products that not only last longer but are engineered for maximum strength and quality. Contact us today for more details.