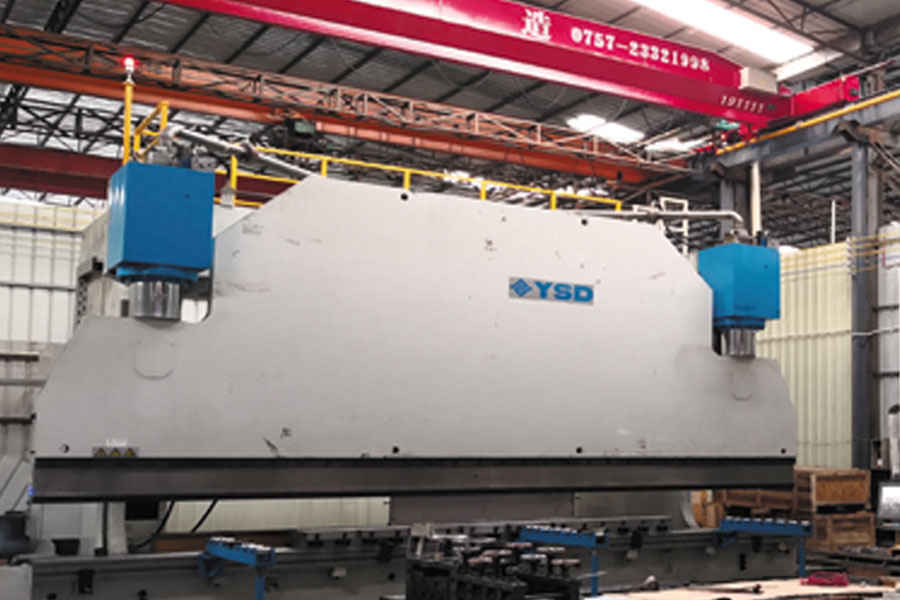
Due to the cnc machining characteristics of the expanding connecting rod, in order to prevent the deformation of the big head hole during the expanding process and at the same time have sufficient strength, the amount of ferrite must be controlled below 10%, and the grain size must not be low at the expanding part. At level 3, the rod part must not be lower than level 5, and the mechanical properties must meet the requirements specified in Table 3-7-3. The material properties are important, but the control of the forging process also plays a very important role, especially the forging process. The control of the medium temperature and the control of the cooling rate are very important to achieve the above requirements.
According to the process parameters provided by Volkswagen, the heating temperature of C70S6 material is 1230C~1260℃, and the temperature after forging is above 900℃, and then it enters the controlled cooling line for cooling. In the test, we found that the lower the forging heating temperature, the finer the grain size, the lower the yield and tensile strength, the higher the elongation and the reduction of section; the higher the temperature, the coarser the grain size, the higher the yield and tensile strength, The elongation and reduction in area become lower. In order to improve the effect of expansion, the grain size at the expansion part should not be lower than grade 3. If the grain size is coarser, slag will easily occur during the expansion process, which will lead to the scrapping of the connecting rod.
In order to meet the performance requirements of the above-mentioned expanding connecting rod, a certain cooling rate is required after forging, and the purpose is to control the precipitation of ferrite. If the ferrite content is too high, the strength will decrease. When the connecting rod is assembled, the cover is combined with the body. The surface will be deformed and the big head hole will be out of round, resulting in the phenomenon of local wear as shown in Figure 3-7-1.