Forged aluminum is a versatile and widely used material in various industries, known for its exceptional strength-to-weight ratio, durability, and excellent mechanical properties. The forging process enhances the material’s properties, making it an ideal choice for critical applications that require high strength and reliability. In this article, we will explore what forged aluminum is, delve into the forging process, examine the advantages it offers, and explore the wide range of applications across industries.
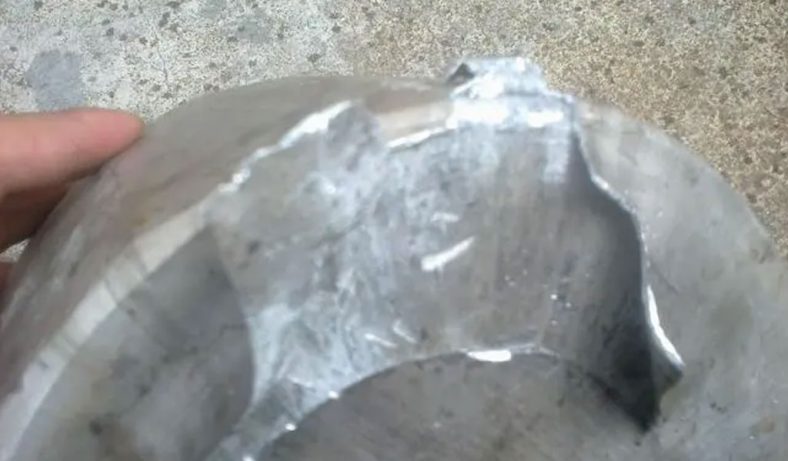
What Is Forged Aluminum – The Define Of Forged Aluminum
Forged aluminum is a type of aluminum that has undergone a specific manufacturing process called forging, which imparts enhanced strength, durability, and mechanical properties to the metal. The forging process involves applying compressive forces to the aluminum to shape it into desired forms, resulting in a refined microstructure and improved material properties. Forged aluminum is widely used in various industries due to its exceptional strength-to-weight ratio, making it an ideal choice for applications that require high-performance and lightweight materials.
The Type Of Metal Forging
The forging process involves subjecting the metal to compressive forces to shape it into the desired form. Forged aluminum is typically created using two primary forging methods:
- 1. Open-Die Forging: In open-die forging, the aluminum workpiece is heated and placed on a flat anvil, while the hammer or press delivers repeated blows to shape the metal. The metal is gradually worked into the desired shape by controlling the force and direction of the blows. Open-die forging is suitable for producing large, heavy, and relatively simple shapes.
- 2. Closed-Die Forging: In closed-die forging, the aluminum is placed within a die, which contains a cavity that matches the shape of the desired final product. The metal is then subjected to compressive forces to fill the die cavity and take its shape. Closed-die forging is suitable for producing complex and intricate shapes with high precision.
Both open-die and closed-die forging can be further classified into hot forging, warm forging, and cold forging, depending on the temperature at which the metal is processed. Hot forging involves heating the aluminum above its recrystallization temperature, warm forging involves processing at a temperature below recrystallization but above room temperature, and cold forging is conducted at room temperature.
Advantages of Forged Aluminum
Forged aluminum offers numerous advantages over other manufacturing processes and materials, making it a preferred choice for critical applications in various industries:
- High Strength-to-Weight Ratio: Forged aluminum exhibits exceptional strength-to-weight ratio, making it an ideal choice for aerospace, automotive, and other applications where lightweight materials with high strength are required.
- Improved Mechanical Properties: The forging process refines the microstructure of the aluminum, resulting in improved mechanical properties such as higher tensile and yield strength, toughness, and fatigue resistance.
- Enhanced Durability and Reliability: The compressive forces during forging eliminate internal defects and porosity, enhancing the material’s durability and reliability.
- Precise Dimensional Accuracy: Forging allows for precise shaping and dimensional accuracy, making it suitable for applications where tight tolerances are crucial.
- Consistent Material Properties: Forged aluminum exhibits consistent material properties throughout the entire component, ensuring uniformity and reliability in the finished product.
- Reduction in Material Waste: The forging process generates less material waste compared to other manufacturing methods, contributing to cost-efficiency and sustainability.
- Cost-Effective for High-Volume Production: Forged aluminum is cost-effective for high-volume production due to its ability to produce complex shapes with minimal material waste.
- Impact and Fatigue Resistance: Forged aluminum is highly resistant to impact and fatigue, making it suitable for applications subject to repetitive loading and high-stress environments.
Applications of Forged Aluminum
Forged aluminum finds extensive applications in various industries where high strength, lightweight, and durability are essential requirements:
- Aerospace Industry: Forged aluminum is widely used in aerospace applications, including aircraft frames, landing gears, wing components, and engine parts. Its high strength-to-weight ratio and excellent fatigue resistance make it ideal for enhancing aircraft performance.
- Automotive Industry: In the automotive industry, forged aluminum is used for critical components such as suspension automotive forging components, wheels, steering knuckles, and transmission parts. Its lightweight nature contributes to fuel efficiency and improved vehicle performance.
- Marine Industry: Forged aluminum is utilized in marine applications, including boat hulls, propellers, and marine engine components, due to its corrosion resistance and lightweight properties.
- Defense Industry: The defense industry uses forged aluminum in various applications, including military vehicles, weapon systems, and ammunition components, where high strength and durability are crucial.
- Sports Equipment: Forged aluminum is employed in the manufacturing of sports equipment, such as baseball bats, golf club heads, and bicycle frames and more bike forging parts, to provide athletes with high-performance and durable products.
- Construction Industry: Forged aluminum is used in the construction industry for architectural structures, bridges, and building components, benefiting from its high strength and corrosion resistance.
- Electrical Industry: Forged aluminum is utilized in electrical conductors, connectors, and heat sinks, where lightweight materials with excellent conductivity and heat dissipation are required.
- Medical Devices: In the medical industry, forged aluminum is employed in the production of surgical instruments and prosthetics, taking advantage of its biocompatibility and lightweight nature.
Forged aluminum is a highly versatile and valuable material known for its exceptional strength-to-weight ratio, improved mechanical properties, and superior durability. The forging process further enhances the material’s performance, making it a preferred choice for critical applications in aerospace, automotive, marine, defense, and various other industries. As technological advancements continue, the use of aluminum forging is expected to expand, unlocking new possibilities and applications in precision engineering and high-performance manufacturing. The combination of its mechanical properties, reliability, and lightweight nature positions forged aluminum as a key material for advancing modern industries and shaping the future of precision manufacturing.
How To Forge Aluminum
Forging aluminum involves shaping the metal using controlled compressive forces to enhance its mechanical properties. The forging process can be performed through different methods, such as open-die forging and closed-die forging, each suited for specific applications. Below is a step-by-step guide on how to forge aluminum using the closed-die forging method:
Step 1: Preparing the Aluminum Billet
Start by selecting a high-quality aluminum billet or ingot that matches the desired final shape of the forged component. The billet should be free from any surface defects or impurities that could affect the forging process and the quality of the final product.
Step 2: Heating the Billet
Heat the aluminum billet to the appropriate forging temperature. The temperature depends on the specific aluminum alloy being used, but it generally ranges from 300°C to 500°C (570°F to 930°F). The precise temperature is critical for achieving the required plasticity of the aluminum during the forging process.
Step 3: Placing the Billet in the Die
Once the billet reaches the desired temperature, quickly transfer it to the closed die. The die contains a cavity that corresponds to the shape of the final forged component.
Step 4: Applying Compressive Forces
Apply compressive forces to the heated billet within the closed die. This can be achieved using a hydraulic press or a mechanical hammer. The forces deform the aluminum, causing it to fill the die cavity and take the shape of the desired component.
Step 5: Repeating the Process
Depending on the complexity of the forged component, multiple forging cycles may be necessary to achieve the desired shape and dimensions. Each cycle further compresses and shapes the aluminum until the final form is obtained.
Step 6: Cooling the Forged Component
After the forging process is complete, allow the forged aluminum component to cool gradually in the die. This controlled cooling helps prevent cracking or distortion of the material due to rapid temperature changes.
Step 7: Removing the Forged Component
Once the forged aluminum component has cooled to a suitable temperature, carefully remove it from the die. Inspect the component for any defects or imperfections that may have occurred during the forging process.
Step 8: Post-Forging Treatment (Optional)
Depending on the specific requirements of the application, the forged aluminum component may undergo additional treatments, such as heat treatment or surface finishing, to further enhance its mechanical properties and appearance.
It is essential to maintain precise control over the forging temperature, forging force, and cooling rate to achieve the desired mechanical properties and dimensional accuracy of the forged aluminum component. The closed-die forging process offers superior precision and the ability to produce complex shapes with tight tolerances, making it suitable for various high-performance applications in aerospace, automotive, defense, and other industries.