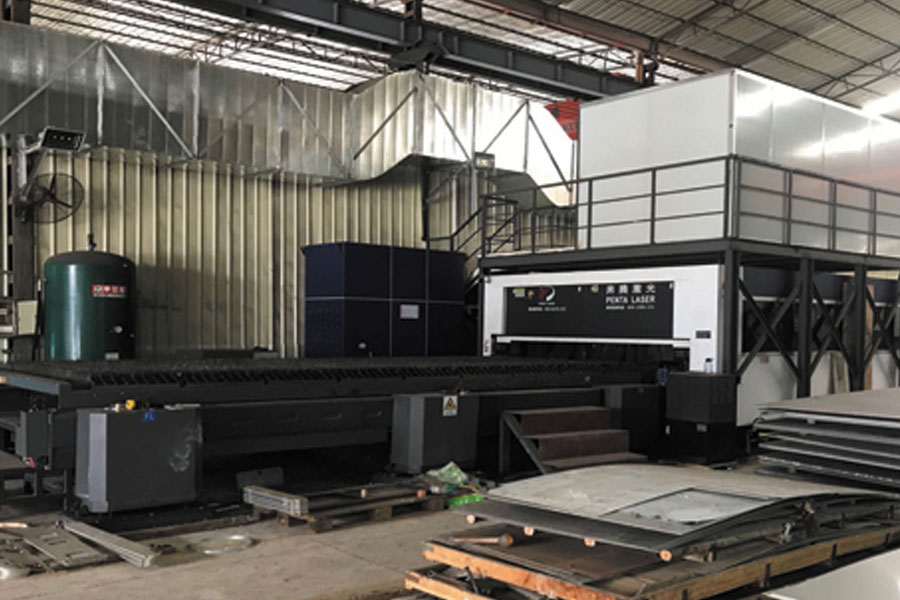
That is, 3 radial inclined parting surfaces and 2 axial oblique parting surfaces. However, the inclined parting surface (guide surface) transitioning from the parting surface of the vertical crank journal to the parting surface of the main journal has 4 axial oblique parting surfaces, but no radial oblique parting surface.
In order to reduce the height of the flange of the neutral cavity between the two balance blocks of the crankshaft and the depth of the cavity of the two balance blocks, to improve the strength of the flange of the mold and to facilitate the filling of the cavity with metal. The parting surface of the non-vertical crutch journal is offset upward by 10.2mm, and the parting surface of the vertical crutch journal is offset downward by 17.3mm
The direction of the radial parting surface is the direction of the three radial parting surfaces of each non-vertical turn marked in the hot forging drawing, which is translated from the parting surface of the inner connecting rod journal of the crank turn with an offset of 10.2mm, and is translated across the vertical centerline of the main journal. 5.1mm, and then the slope of 60° rises to the main journal parting surface, and the two offset 10.2mm crank outer connecting rod journal parting surfaces rise to the main journal parting surface along the outer side of the crank arm with a slope of 60°, that is, there are three A 60° radially inclined parting surface (guide surface) has no radial parting surface direction at the vertical turn.
Axial parting surface direction
Each non-vertical crank has two axially inclined parting surfaces, which are inclined parting surfaces that transition from the parting surface of the connecting rod journal offset by 10.2mm to the parting surface of the main journal at both ends of the crank crank by 15° in the axial direction.Generally, the width of the main journal and the shape of the crankshaft are reasonably allocated. According to the axial dimension of the hot forging of the crankshaft, the width is 21.6mm, which is suitable for production practice.
Each vertical turn has four axial inclined parting surfaces, which are inclined parting surfaces that transition from the 17.3mm offset between the connecting pin parting surface and the intersection of the crank arm to the main journal parting surface and the intersection of the crank arm. The die face slope is 3217. 4) Mark the size of the parting surface direction on the general drawing of the mold
The dimension of the parting surface is marked by the hot forging drawing. It can be seen from Figure 2-6-16 that the axial dimension marked on the hot forging drawing is the axial dimension of the connecting rod auxiliary neck and the main shaft auxiliary neck, and the connecting rod auxiliary neck and the main shaft pair. The axial dimension from the neck to the crank arm is 3.3mm, and the curved surface of the BPD six-turn 8 balance block is divided into the crankshaft. The dimensions of the two ends of the face direction are 152.5+3.3=15.8mm, 258.6-3.3=255.3mm (Fig. 2-6-16), and the dimensions of the parting faces of other bends are analogous.
All guide surfaces are rounded to R8, and the tolerance of all guide surfaces is ±0.2mm.