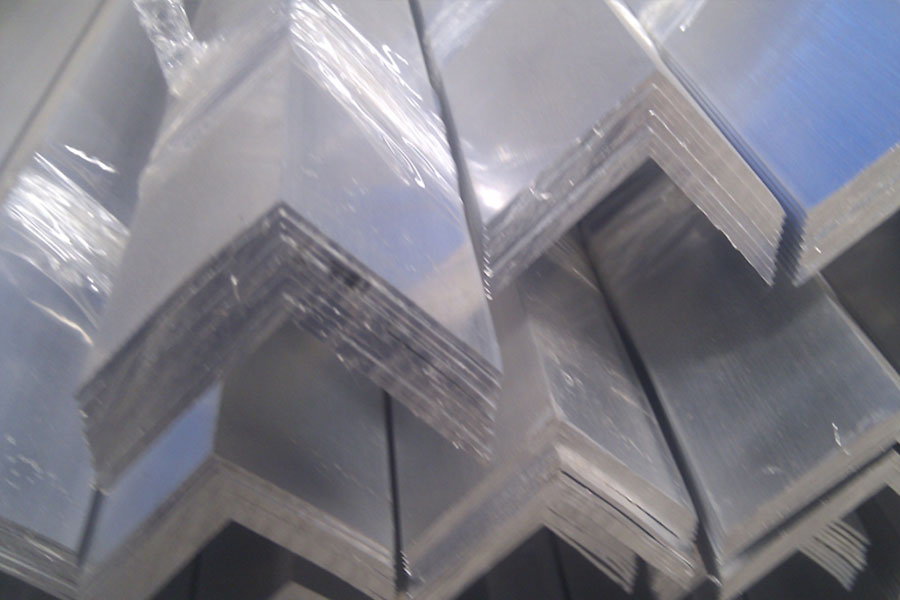
The development of a new forging product should achieve process stability, high material utilization, high die service life and high productivity. This is also the eternal goal of forging enterprises, and it is an inevitable measure for enterprises to reduce the cost of forgings and improve the economic efficiency and competitiveness of enterprises.
Stable process and good forming
First of all, the process should be stable and the forming should be good. That is to say, the forgings are easy to be filled, not folded or deformed during production, and the forgings have excellent structure and performance, so they are required to have very few defective products and a low rejection rate. Process stability is the basic guarantee for improving labor productivity and realizing mechanization. Therefore, in the design of forging process and die, in addition to the grasped laws of metal plastic deformation, numerical simulation and, if necessary, physical simulation are also required.
In order to prevent the trimming deformation of the connecting rod, in the design of the final forging step, the corresponding deformation dimension can be reversely compensated, or a trimming die with an elastic pressing device can be used.
In order to ensure that the balance weight of the crankshaft is full, the pre-forging process should design “integrated skin” between the balance weights and design resistance ribs at the stopper of the balance weight. Bending blanks are prone to folds during crankshaft pre-forging or final forging die cavity forging. In order to avoid folds, not only should the contour folds of the bending blanks be designed with a smooth transition, but also the parts with long metal flow distances should be compensated, and there should be Accurate positioning.
In order to ensure that the long forks of the vertical forging extrusion steering knuckle are full, the volume of the pre-forging blanks and the design resistance ribs are reasonably distributed to form the extrusion cavity.