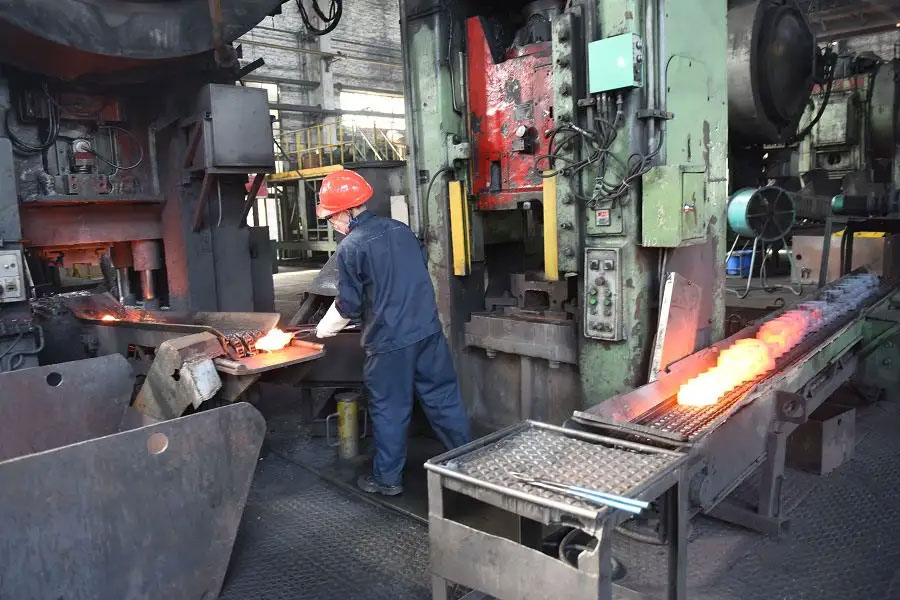
The white spot and hydrogen embrittlement defects of large forgings are very harmful, so the heat treatment to prevent white spot and hydrogen embrittlement is required after forging of large forgings. At the same time, the forging stress is removed, the hardness is reduced and the grain is refined. Now we write down our understanding of white spots related to post forging heat treatment of large forgings for reference.
1 The Basic Concepts Of White Spots In Steel
- 1.1 harmfulness of white spot white spot is an internal crack caused by hydrogen in steel. When the hydrogen content in solid steel is too high, the steel becomes significantly brittle. In essence, white spot also belongs to brittle failure. The existence of white spots sharply reduces the mechanical properties of steel, especially the transverse plasticity and toughness, and becomes the most dangerous fracture source, which seriously affects the service performance and service life of parts. Therefore, once a white spot is found in the forging, the forging must be scrapped.
- 1.2 the appearance of white spots on the longitudinal fracture surface of the forging presents as round or oval silvery white spots with clear edges; On the transverse low magnification test piece, it is a hairy small crack, with a length of several millimeters and a maximum of tens of millimeters.
- 1.3 conditions and formation temperature of white spots are produced under the combined action of hydrogen and stress (deformation stress, thermal stress, microstructure stress, especially microstructure stress) in steel after forging. The formation temperature of white spots is about 250 ℃ to room temperature when the forging blank is cooled to a relatively low temperature.
- 1.4 the relationship between hydrogen and stress in the formation of white spots the author of document [2] pointed out: “the existence of sufficient hydrogen in steel is the necessary condition for the formation of white spots, and the existence of internal stress can promote the formation of white spots. Therefore, the supersaturated hydrogen content is the ‘culprit’ of white spots, while the internal stress is the ‘accomplice’.” Very thoroughly said the relationship between the two white spots.
- 1.5 three characteristics of white spots 1) white spots are never formed on the surface of forgings. According to relevant data, it is always formed inside the forging, and the area containing white spots is always a considerable distance from the forging surface, about 5O mm; 2) White spots are formed after forging when the forging is cooled to a relatively low temperature of 250 ℃ to room temperature; 3) White spots are not formed instantaneously, but gradually. From stopping forging to the appearance of white spots, it takes a period of time, which is called the incubation period or incubation period of white spot formation. The length of incubation period depends on the hydrogen content of steel and the thickness of forgings.
Post Forging Heat Treatment Of Large Forgings The Heat Treatment Immediately After Forging Is Called Post Forging Heat Treatment.
The purpose of post forging heat treatment of large forgings is to remove stress, recrystallize, refine grain and remove hydrogen at the same time.
2.1 recrystallization treatment large forgings undergo multiple recrystallization treatment to refine grains, improve microstructure and improve properties.
2.2 Dehydrogenation Annealing will reduce the hydrogen in forgings to below the limit hydrogen content and make it evenly distributed to avoid the risk of white spots and hydrogen embrittlement. Due to the different solubility and diffusion coefficient of hydrogen in phase 7 and phase a, especially the low solubility and large diffusion coefficient of hydrogen in phase a, hydrogen can continuously diffuse outward during annealing. Dehydrogenation Annealing is often combined with recrystallization. The temperature of Dehydrogenation Annealing is usually 650 ℃. After annealing, it shall be cooled as slowly as possible to prevent new internal stress. Generally, the cooling is divided into two stages: above 400 ℃, the cooling can be faster because the plasticity of the steel is good and the internal stress is not easy to form; Below 400oC, the cooling speed will slow down. For forgings with many alloy elements and high performance requirements, one or even multiple recrystallization heat treatment is required after forging, so as to improve the microstructure and properties of forgings.
3 Ways And Measures To Reduce Hydrogen Content in steel Forgings Of Different Steel Grades Have Different Sensitivity To White Spots.
The main factor affecting the sensitivity of forgings is the hydrogen content of steel. The higher the hydrogen content of steel, the greater the white spot sensitivity. Hydrogen in steel can exist in atomic state, molecular state or compound state. Atomic hydrogen plays a decisive role in the formation of white spots. The fundamental way to prevent white spots is to reduce the hydrogen content of steel and limit the residual hydrogen in steel below the limit hydrogen content without white spots.
3.1 main ways to reduce hydrogen content in steel
- Vacuum degassing or vacuum casting of molten steel in steelmaking. Electroslag remelting process can be used to further improve the purity of steel for some forgings with higher requirements.
- Post forging heat treatment: Dehydrogenation Annealing to diffuse the hydrogen in the steel.
3.2 measures to prevent white spots the methods to prevent the formation of white spots in steel include two aspects:
- first, try to minimize the hydrogen content in liquid steel and create conditions to make hydrogen diffuse and escape from billet; The second is to reduce the internal stress, especially the structural stress, generated in the billet during cooling.
- In order to reduce the hydrogen content of steel, scrap steel with serious corrosion shall be used as little as possible or not used in smelting;
- Use freshly roasted or heated lime; Use heated ferroalloy;
- Steel making tools shall be fully dried and baked, and the casting system shall be dry;
- The temperature of molten steel shall not be too high to avoid excessive absorption of hydrogen, and ensure long enough and powerful boiling of molten steel to facilitate dehydrogenation.
The slag shall not be too thin, and the final slag shall be appropriately viscous, etc.
The hydrogen content requirements of Dehydrogenation Annealing are not required for large forgings after forging
- Control the hydrogen content of steel. The hydrogen content of forgings is generally recognized as (2-3) in relevant industries (forging and heat treatment) at home and abroad × Below 10, white spots can be avoided. Therefore, 1) for general large forgings, hydrogen content ≤ (2) × 10:00; 2) For important large forgings, hydrogen content (1 ~ 1.5) × At 1o. At this time, the hydrogen content in the steel has fallen below the limit hydrogen content without white spots, so there will be no white spots. Post forging heat treatment and Dehydrogenation Annealing can not be done, but recrystallization must not be ignored. Post forging heat treatment and Dehydrogenation Annealing is the product of backward smelting process and low level of molten steel in smelting.
- At present, the purity level of special steel in China. The purity of molten steel is the key link to ensure the quality of forgings. At present, China’s major special steel enterprises have greatly improved their production process and technical level through the introduction of production equipment and technological transformation. The usual smelting method is: electric furnace roughing + secondary refining. The methods of secondary refining usually include powder spraying, vacuum carbon deoxidation (VCD), ladle refining (VaD, CF), atmospheric oxygen argon decarburization and electroslag remelting. Through secondary refining, hydrogen, oxygen and nitrogen in steel can be controlled at a very low level. At present, the purity can reach ~ ijeh] ≤ (2) × lo~、[o]≤(15) × Lo I. [n] ≤ (5O) × lo_。。; The purity has reached the international advanced level. When the hydrogen content of forgings is (3 ~ 7 or higher) × Lo, there is no doubt that the post forging heat treatment of large forgings must be post forging Dehydrogenation Annealing immediately after forging.
5 Example Of Eliminating Hydrogen Annealing After Forging Of Large Forgings
1) Shandong Jinan YILAITE Heavy Industry Co., Ltd.
Shandong Jinan YILAITE Heavy Industry Co., Ltd. is a large forging enterprise jointly invested and established by Spain haistamp group. It provides ring grinding processing of wind power gear ring forgings in strict accordance with various processes such as “blank making, ring forging, heat treatment, machining and flaw detection”. YILAITE has made strict regulations on the hydrogen content of the steel used, and the hydrogen content is ≤ (1 ~ 1.5) × 10 1. The generation of white spots can be completely avoided, so the post forging heat treatment does not do Dehydrogenation Annealing. The company has many foreign orders. So far, no forging with white spots due to the failure of post forging heat treatment Dehydrogenation Annealing has been found, and there are no scrapped products with white spots due to the failure of post forging heat treatment Dehydrogenation Annealing.
2) Hebei Huigong mechanical equipment Co., Ltd.
Hebei Machinery Co., Ltd. is a professional manufacturer of PTO engine assembly, gearbox assembly and heavy-duty truck gearbox assembly. Drawing on the advanced experience of American gear industry in post forging heat treatment of large metal forgings, when purchasing steel and signing technical agreements with relevant domestic special steel enterprises, our company clearly puts forward the requirements for steel purity: I-h] ≤ (2) × 10 I. [O] ≤ (15) × 10~、[N]≤(5O) × 10~。 For large forgings, the hydrogen content shall be further controlled within ≤ (2) × 10 and ≤ (1 ~ 1.5) × Between 10, the generation of white spots can be avoided. Therefore, the requirement of Dehydrogenation Annealing is no longer put forward to the forging plant, but only one or two recrystallization heat treatments. Up to now, there has been no malignant accident of forging white spots and product scrapping due to no Dehydrogenation Annealing. In addition, the gears produced by these forgings have been in normal use for a long time.
(3) FAW and Erqiao automobile factory (company).
As far as I know, the gears produced by the axle factory (company) of faw-2 in China have strict requirements on the purity of gear steel. Therefore, the forgings are also exempted from dehydrogenation annealing after forging.
6 Precautions In Post Forging Heat Treatment Of Large Forgings
(1) Procurement and storage of steel.
When purchasing steel, it should be selected in the seasons of spring, summer, autumn and winter. In order to ensure that the steel meets the standard in terms of purity and avoid the impact of plum rain season on steel every year, there should be a certain amount of reserves in the quantity of steel, which should be prepared for urgent need on the premise of ensuring the quality.
(2) Sensitivity of white spots.
During the cooling process of forgings, the hydrogen on the surface is easy to diffuse and escape, while the hydrogen in the heart is not easy to discharge. Therefore, the larger the section of the forging, the easier it is to produce white spots. With the increase of forging section, the degree of steel segregation is more serious, which is easier to promote the formation of white spots. The larger the surface area of the forging, the easier it is to precipitate hydrogen. Therefore, hollow forgings (such as gear rings) are less sensitive to white spots than solid forgings (such as gear shafts). Low carbon steel with carbon content less than 0.3 has very low white spot sensitivity. With the increase of carbon content, the white spot sensitivity of steel increases. The faster the cooling rate after forging, the greater the white spot sensitivity.
- Steel without white spots: such as austenitic steel, ferritic steel, AUSTENITIC FERRITIC STEEL AND ledeburite steel. Under normal production conditions, carbon steel with carbon content less than 0.39/6 and manganese content less than 0.6 will not form white spots. Therefore, it is not necessary to conduct Dehydrogenation Annealing after forging for this kind of steel;
- Steel sensitive to white spots: pearlitic steel is less sensitive to white spots, martensitic pearlitic steel is more sensitive to white spots, and martensitic steel is the most sensitive to white spots. Such as 20cr2ni4, 18Cr2Ni4W, 20CrNi2Mo, 40CrNi2Mo, 40CrNiMo, etc. The limit hydrogen content of martensitic steel white spot is ≤ (1.8) × l0~。
- Heavy forgings that have been scrapped due to white spots shall be changed. The forgings with white spots can be processed into parts with smaller size by hot processing methods such as forging modification. The small-size billet after forging modification needs slow cooling and annealing, which can recover part of the scrapped steel.
- Quality inspection report shall be provided at the same time of delivery of forgings.
When delivering forgings, the forging factory must issue:
- 1) Purity RH], [n], [O] content;
- 2) Chemical composition and mechanical properties;
- 3) Forging ratio;
- 4) Quality inspection report of ultrasonic flaw detection and other related contents.