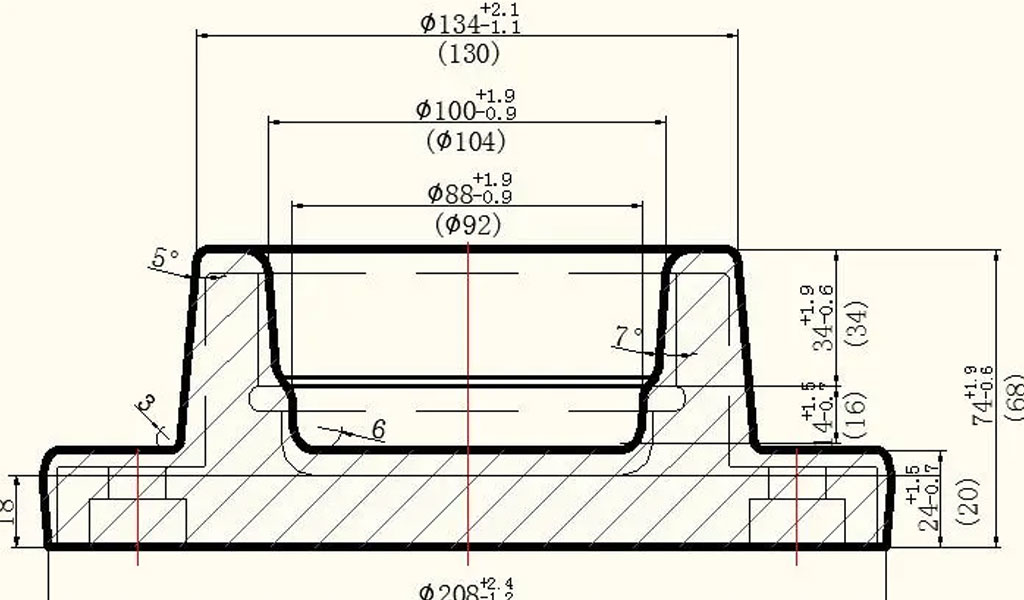
With the rapid development of the forging industry, the design of the forging drawing needs to consider the machining allowance, rolling tolerance, rolling residual block and so on. These aspects need the attention of the majority of enterprises (forging plants).
- The design of forgings involves four aspects:
- That is, the requirements of the forging pressure on the shape and structure of the forging, and the material of the forging should be selected correctly;
- The process performance of the forgings, and the dimensional accuracy of the forgings is reasonably determined;
- For the dimensional accuracy and surface requirements of the forgings, try to make the wall thickness distribution uniform;
- To determine the parting surface of the forging, add a process fillet at the corner to avoid sharp corners. The design of forgings is an important part of forging production technology. The following issues must be considered in the design: the selection of the mold parting surface, the opening of the gate, the selection of the position of the ejector, the guarantee of the dimensional accuracy of the forgings, and the prevention of the internal defects of the forgings. Requirements , the relevant requirements of shrinkage deformation and the size of the machining allowance.
- Shape and structure requirements of forgings:
- Eliminate internal side concave;
- Avoid or reduce core pulling parts;
- Avoid core crossing; a reasonable forging structure can not only simplify the forging structure, reduce the manufacturing cost, but also improve the forging quality.
- Wall thickness requirements for forging design:
The wall thickness of the forging is a factor of special significance in the forging production process. The wall thickness is closely related to the entire process specification, the effect of pressure, the length of the mold retention time, the ejection temperature of the forging and the operating efficiency. With the increase of wall thickness of forgings, the internal defects such as pores and shrinkage holes increase. Therefore, under the premise of ensuring sufficient strength and rigidity of forgings, the wall thickness of forgings should be reduced as much as possible and the thickness of the section should be kept uniform.