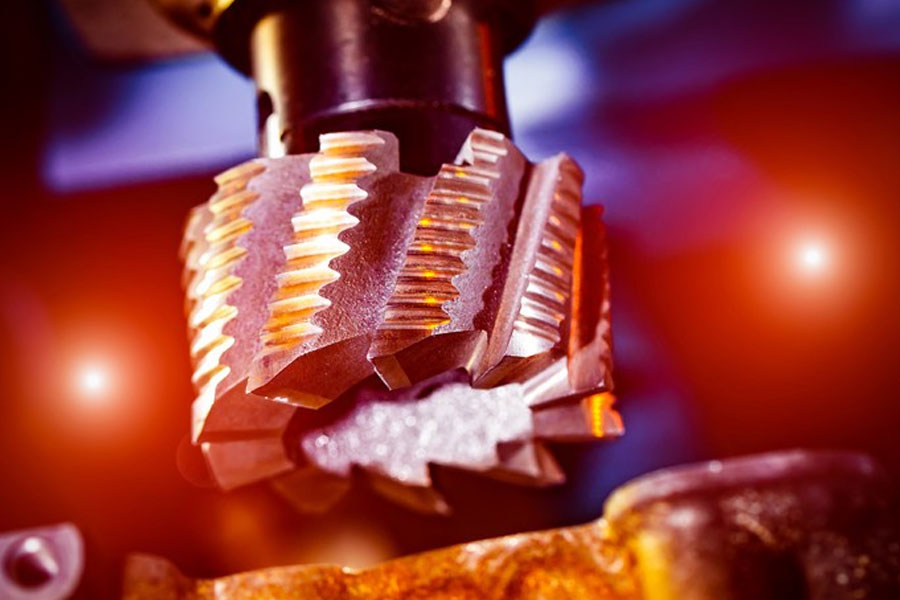
KMS connecting rod forging weighs 2.78kg, mold material is 4Cr5 MosiN, and mold hardness is HRC46~HRC49
Module → heat treatment → rough EDM → fine EDM → grinding and polishing. Each forging die is processed for about 15 hours, which does not include the preparation and production time of rough and fine electrodes.The cavity accuracy is up to 0.05mm, and the roughness is Ra1.6m1A
When the old mold is refurbished, the outstanding advantages of the high-speed milling machining center are revealed. According to the original mold-making process, the old mold can be directly milled down a few millimeters, and it becomes a new mold. For example, a company forged the center hole on the screw press. Similar steering knuckle, the mold has been refurbished many times, and the total life of the mold is 100,000 pieces
In short, with the development of the automobile industry and a new round of technological innovation, development opportunities and technological progress have been brought to the forging industry. In recent years, advanced technologies have appeared in various forging processes and equipment. That is to say, all aspects of raw materials, blanking, heating, die forging and its dies, lubrication, heat treatment, cleaning and testing have made great progress. The above description is only the main part. The general development trend of the forging industry should be “three modernizations”, “three improvements” and “three reductions”. For this reason, many advanced manufacturing technologies will continue to emerge in the forging industry. Along (1) Three modernizations: precision of forging size, specialization of production varieties, and high efficiency of productivity.
Three improvements: improve the utilization rate of materials, increase the service life of the die, and improve the microstructure and properties of the forgings. ,, 3 (3) Three reductions: reduce the comprehensive energy consumption of forgings, reduce environmental pollution, and reduce the cost of forgings.