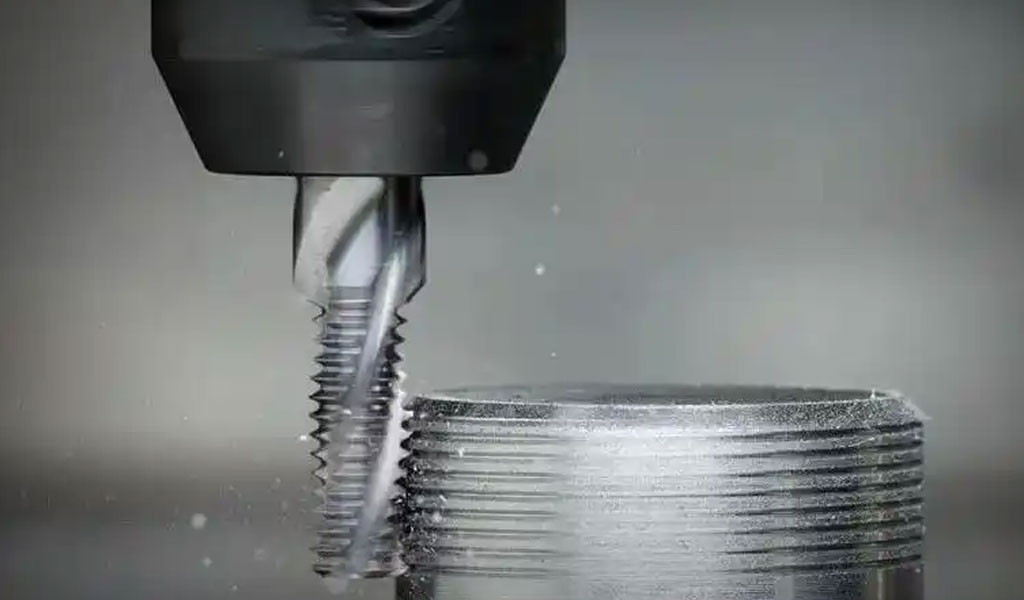
Thread milling technology is an advanced method used in CNC machining centers for the production of threaded holes with high precision and efficiency.
Unlike traditional tapping methods, which use a single-point tap to create threads, thread milling involves a rotating tool that moves along the contour of the thread.
This technology has found widespread applications in a variety of industries, including aerospace, automotive, medical, and defense, due to its versatility and the precision it offers.
Thread milling allows for the production of both internal and external threads, with the ability to create complex thread forms such as left-handed, right-handed, and custom profiles. The process is characterized by its ability to create threads in materials of varying hardness and geometries, making it a vital tool for modern machining operations.
Overview of Thread Milling Technology
Thread milling utilizes a multi-flute cutter, typically with helical cutting edges, which moves around the periphery of the hole to form the desired thread profile. The cutter engages the material progressively, and the tool path can be adjusted to accommodate various thread types and sizes. Thread mills come in various designs, including solid carbide, carbide insert, and high-speed steel (HSS) versions, each suitable for specific machining conditions and material types.
One of the key advantages of thread milling over tapping is its ability to handle deeper threads. In tapping, the length of the thread is limited by the tool’s ability to maintain alignment and strength during operation. Thread milling, on the other hand, can produce threads of greater depth without the same risk of tool breakage or misalignment. This makes it especially beneficial for applications involving deep holes or those requiring high-strength materials, such as aerospace components.
Thread milling can be applied to both blind and through holes, and it offers superior chip evacuation compared to tapping. This is particularly important when machining materials with high cutting resistance or materials that tend to work-harden during the cutting process, such as stainless steel or titanium alloys. Additionally, thread milling offers greater flexibility in tool selection, as multiple tools can be used to produce different thread types, reducing setup times and tool changes during a machining operation.
Technical Aspects of Thread Milling in CNC Centers
Thread milling in CNC machining centers is controlled through advanced G-code programming, allowing for the precise control of the tool path, feed rates, and cutting speeds. CNC thread milling operations require accurate machine settings to ensure that the tool follows the exact contours of the desired thread form. The CNC machine’s software calculates the optimal movement of the tool, factoring in variables such as the material being cut, the diameter and pitch of the thread, and the machine’s capabilities.
The thread milling process involves several stages: pre-drilling, thread milling, and finishing. Initially, a pilot hole is drilled to a predetermined diameter, ensuring that the tool can properly follow the required path. The thread mill then moves around the hole, cutting the material layer by layer to create the thread. The depth and form of the thread are controlled by adjusting the tool’s axial and radial movements.
Unlike tapping, which typically requires a single-direction movement of the tool, thread milling requires a combination of radial and axial tool movements to achieve the desired thread profile. This motion is often referred to as a “helical interpolation,” where the tool moves in a helical pattern to cut the thread. The number of passes the tool makes depends on the material and the desired thread depth.
Advantages of Thread Milling
- Versatility: One of the most significant benefits of thread milling is its versatility. CNC thread mills can create a wide range of thread types, including but not limited to, unified, metric, NPT, and BSP threads. This versatility makes thread milling an ideal solution for applications requiring a variety of thread forms. Additionally, thread milling can produce both internal and external threads, which adds to its flexibility in manufacturing.
- Precision and Accuracy: Thread milling is a highly accurate process that ensures tight tolerances for threaded holes. With CNC technology, thread mills can achieve excellent thread pitch consistency and form accuracy, which is crucial in industries such as aerospace, automotive, and medical device manufacturing, where precision is paramount. Furthermore, CNC thread milling allows for easy compensation for tool wear, ensuring the consistent quality of the threaded holes.
- Material Capability: Thread milling can be applied to a wide variety of materials, including soft materials like aluminum, hard metals like stainless steel, and high-strength alloys like titanium. The ability to mill threads in hard materials is particularly advantageous in industries such as aerospace and defense, where high-performance components are often made from challenging materials. Thread milling can also handle materials that are prone to work hardening, such as Inconel or other nickel-based alloys, without causing tool wear or part defects.
- Chip Control and Evacuation: In tapping, chips can become trapped in the tool or in the hole, leading to thread defects, increased wear, and poor surface finishes. Thread milling, however, allows for better chip control and evacuation, as the cutter’s design and movement ensure that chips are efficiently removed from the cutting area. This reduces the risk of clogging, overheating, and tool damage, leading to longer tool life and improved process reliability.
- Tool Life and Durability: The use of carbide and other durable tool materials in thread milling tools enhances tool life. In addition to longer tool life, thread milling enables users to create threads without the need for constant tool changes, as opposed to tapping operations, which often require multiple taps for different sizes and thread forms.
- Reduced Tool Breakage and Downtime: In comparison to tapping, thread milling significantly reduces the risk of tool breakage. Since the tool moves along a helical path, it does not encounter the same cutting forces as tapping. Tapping tools, particularly in deeper holes or hard materials, are susceptible to breakage or misalignment, leading to downtime and expensive part rejection. Thread milling offers a more robust and reliable solution for deep or complex threads.
- Efficiency and Speed: Although thread milling is a multi-pass operation, it can be faster than tapping, especially for deep or difficult threads. By using a CNC machining center to program optimal cutting paths and speeds, thread milling can complete complex threading tasks quickly and with minimal downtime between tool changes. The ability to perform both rough and finish cuts in a single operation further enhances efficiency.
Applications in Industry
Thread milling has widespread applications in industries that require high precision and complex threading operations. These include aerospace, automotive, medical device manufacturing, defense, and energy industries. Below are some specific examples of how thread milling is applied in various sectors:
- Aerospace Industry: In the aerospace sector, thread milling is used for creating critical threads in engine components, turbine blades, and structural parts. These components often need to withstand extreme temperatures, pressures, and mechanical stresses. Thread milling allows for the production of threads in tough materials like Inconel and titanium alloys, ensuring reliable connections in high-performance applications.
- Automotive Industry: Thread milling is commonly employed in automotive manufacturing for components like cylinder heads, transmission cases, and engine blocks. The ability to create accurate, deep threads in tough materials like cast iron and aluminum is essential in ensuring the performance and safety of automotive parts. Thread milling also plays a role in producing components for electric and hybrid vehicles, where precision is critical for components such as battery housings and electric motor parts.
- Medical Device Manufacturing: The medical industry relies on precise threading for components such as implants, surgical tools, and medical devices. Thread milling is particularly useful for creating threads in biocompatible materials like titanium, which is commonly used for orthopedic implants. The high precision of thread milling ensures that threads are created with minimal risk of defects, which is vital for the safety and functionality of medical devices.
- Defense Industry: In defense, thread milling is utilized to create threaded components for weapons, communication devices, and military vehicles. The need for high-strength, precise threads in materials such as hardened steel, alloys, and composite materials makes thread milling an essential technology in the production of defense-related components.
- Energy Sector: Thread milling plays a crucial role in the energy sector, particularly in the production of components for the oil and gas industry. The ability to mill threads in tough, corrosion-resistant materials such as stainless steel and Inconel is vital for the manufacturing of high-performance parts used in drilling equipment, pipelines, and turbines.
Challenges and Limitations of Thread Milling
While thread milling offers several advantages, it is not without its challenges. One of the key limitations of thread milling is the need for specialized tooling and programming. Unlike traditional tapping, which requires a simple tap to create threads, thread milling requires a CNC machine equipped with the appropriate tooling and software to generate the complex tool paths required for thread cutting.
Another challenge is the potential for excessive tool wear, particularly when machining hard or abrasive materials. While thread milling can generally improve tool life compared to tapping, the cutting forces involved in deep thread milling operations can lead to faster wear on the tool, especially when working with materials that are difficult to machine.
Finally, thread milling is often considered a more complex operation compared to tapping, requiring advanced programming skills and expertise in CNC machining. The process involves multi-axis motion and helical interpolation, which may require additional training and experience to master. Furthermore, setting up a CNC machine for thread milling operations may take longer than for traditional tapping, particularly when dealing with multiple thread sizes or complex workpieces.
Conclusion
Thread milling technology is a sophisticated and versatile solution for creating threaded holes in CNC machining centers. Offering greater flexibility, precision, and material compatibility than traditional tapping methods, thread milling is becoming an increasingly important technology in modern manufacturing. Its ability to produce complex, deep threads in a variety of materials has made it essential in industries such as aerospace, automotive, medical device manufacturing, and defense.
While thread milling presents certain challenges in terms of tool wear, setup time, and programming complexity, its advantages in terms of thread quality,