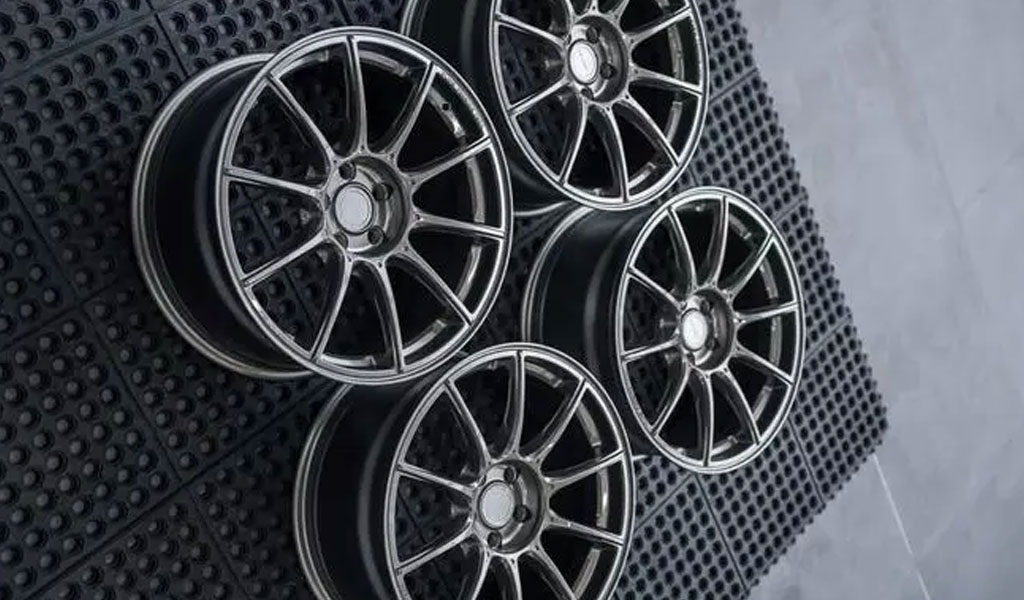
Metalworking processes are crucial in manufacturing industries, offering various methods to shape and manipulate metals for diverse applications. Among these processes, metal forging and metal spinning stand out as significant techniques with distinct characteristics and advantages. This article provides an in-depth comparison of metal forging and metal spinning, exploring their methodologies, applications, advantages, and limitations.
1. Overview of Metal Forging
1.1. Definition and History
Metal forging is a process that involves shaping metal through compressive forces. It dates back to ancient civilizations, where blacksmiths would manually hammer metal into desired shapes. The process has evolved significantly, with modern forging incorporating advanced machinery and techniques.
1.2. Types of Forging
1.2.1. Open-Die Forging
Involves deforming metal between two flat dies, allowing for more complex shapes and sizes. It is suitable for large, heavy components.
1.2.2. Closed-Die Forging
Utilizes pre-shaped dies to produce intricate designs with high precision. It is commonly used for mass production of smaller components.
1.2.3. Drop Forging
Involves dropping a hammer onto the metal, shaping it within a die. This method is efficient for producing high-strength components.
1.2.4. Roll Forging
Metal is passed through a series of rollers to achieve the desired shape. This method is used for producing long, uniform components.
1.3. Forging Process
1.3.1. Heating
The metal is heated to a temperature where it becomes malleable, allowing for easier shaping.
1.3.2. Shaping
The heated metal is then shaped using various tools and dies, depending on the forging method employed.
1.3.3. Cooling
After shaping, the metal is cooled, often in a controlled manner to achieve specific mechanical properties.
1.4. Applications of Forging
Forging is widely used in industries such as automotive, aerospace, and construction. Applications include engine components, structural parts, and tools.
2. Overview of Metal Spinning
2.1. Definition and History
Metal spinning, also known as spin forming, involves shaping metal by rotating it against a tool. This technique has been used for centuries to create symmetrical parts and has seen advancements with the advent of modern machinery.
2.2. Types of Metal Spinning
2.2.1. Manual Spinning
Performed by hand, this method is suitable for small-scale production and custom parts.
2.2.2. Automatic Spinning
Utilizes automated machinery to produce large quantities of parts with high precision.
2.3. Spinning Process
2.3.1. Setup
The metal blank is mounted on a spindle and rotated at high speeds.
2.3.2. Forming
A tool is applied to the rotating metal, shaping it into the desired form. This can involve various techniques, including pressure forming and centrifugal forming.
2.3.3. Finishing
Post-spinning, the component may require additional finishing processes, such as trimming and polishing.
2.4. Applications of Spinning
Metal spinning is commonly used in industries such as aerospace, automotive, and decorative arts. Applications include aircraft components, automotive wheels, and decorative items.
3. Comparison of Metal Forging and Metal Spinning
3.1. Process Complexity
Metal forging typically involves more complex machinery and higher initial setup costs compared to metal spinning. Forging often requires significant heating and shaping tools, while spinning focuses on rotational shaping.
3.2. Material Utilization
Forging tends to produce less waste compared to spinning, as it can shape the metal more efficiently. However, spinning is advantageous for creating thin-walled, intricate shapes with minimal material loss.
3.3. Mechanical Properties
Forged components generally exhibit superior mechanical properties, including higher strength and durability. Spun parts, while often lighter and more complex in shape, may not match the strength of forged components.
3.4. Production Volume
Forging is suitable for high-volume production, especially in closed-die and drop forging methods. Spinning is more adaptable to low-to-medium volume production, especially for custom and intricate designs.
3.5. Cost Considerations
Forging can be cost-effective for high-volume runs but may require significant upfront investment in tooling and machinery. Spinning, with its lower initial costs, is advantageous for smaller production runs but may become more expensive for large quantities due to higher per-piece costs.
4. Advantages and Limitations
4.1. Advantages of Forging
- Strength and Durability: Forged components typically exhibit higher tensile strength and fatigue resistance.
- Complexity: Capable of producing complex shapes with tight tolerances, especially in closed-die forging.
- Material Efficiency: Generally produces less waste compared to other methods.
4.2. Limitations of Forging
- Cost: High initial tooling and setup costs can be prohibitive for small production runs.
- Material Constraints: Limited to certain materials that can withstand the forging process.
4.3. Advantages of Spinning
- Design Flexibility: Ideal for creating complex, symmetrical shapes with fine details.
- Lower Tooling Costs: Reduced initial costs compared to forging, making it suitable for low-to-medium volume production.
- Material Efficiency: Minimal material waste, especially for thin-walled components.
4.4. Limitations of Spinning
- Strength: Spun parts may not match the strength and durability of forged components.
- Production Speed: May be slower compared to forging for large production runs.
5. Case Studies
5.1. Forging in Aerospace Industry
Exploration of specific examples where forging has been utilized to create critical aerospace components, emphasizing the benefits of strength and reliability.
5.2. Spinning in Automotive Industry
Case studies highlighting the use of metal spinning for automotive parts, focusing on design flexibility and aesthetic considerations.
6. Future Trends and Developments
6.1. Advancements in Forging Technology
Discussion of innovations in forging techniques, including the integration of automation and advanced materials.
6.2. Emerging Trends in Metal Spinning
Examination of recent developments in metal spinning, such as the use of new materials and improved spinning technologies.
7. Conclusion
A summary of the key differences and similarities between metal forging and metal spinning, reiterating their respective advantages and applications.