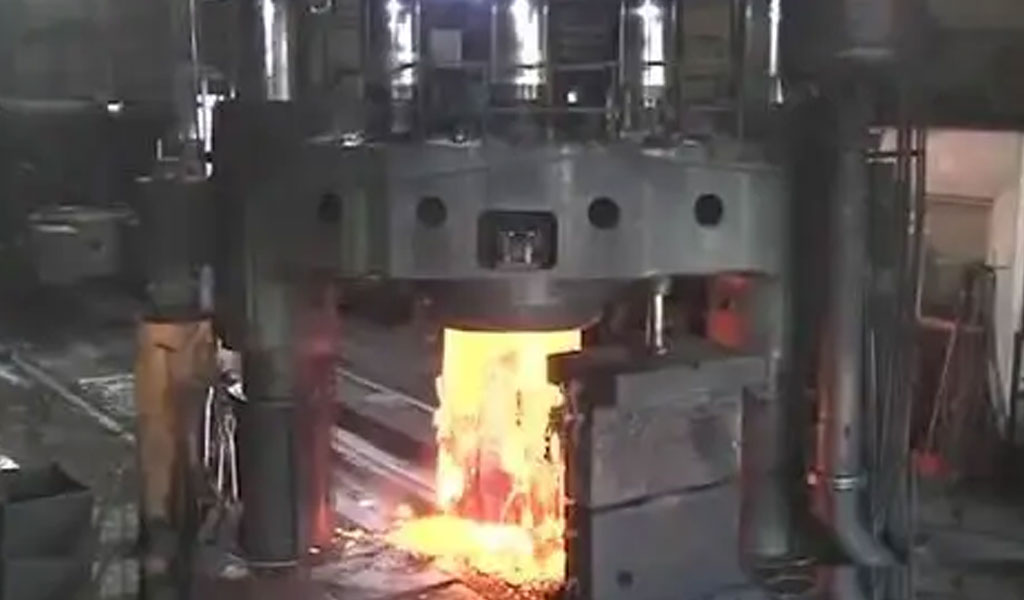
In recent years, with the introduction of automobile energy saving and emission reduction policies, manufacturers have turned their attention to lightweight design and product development of new energy-saving plastic technologies, which have put forward higher requirements for the formation of supporting equipment, which has promoted the forging of aluminum alloy wheels in my country. Development of technology and molding equipment.
Aluminum is one of the most widely used non-ferrous metal structural materials in industry and is widely used in aviation, aerospace, machinery manufacturing, shipbuilding, chemical industry and other fields. Aluminum alloys can be forged in forging equipment such as forging hammers, mechanical presses, presses, upsetting machines, and reamers. Free forging, die forging, upsetting forging, rolling forging, reaming.
When forging aluminum alloy chassis parts of automobiles, the aluminum alloy is usually heated to the forging temperature first, and then plastically deformed after the temperature is stabilized, and solution treatment and timely treatment are carried out after the plastic deformation.
In order to improve the plasticity of the aluminum alloy forging process and reduce the deformation resistance, it is necessary to ensure that the aluminum alloy billet is in a single-phase state. Therefore, in the forging process of aluminum alloy chassis parts of automobiles, it is usually necessary to heat several times to ensure that the aluminum alloy parts are at a proper forging temperature.
In order to fully dissolve the various stages of the aluminum alloy, strengthen the solid solution, improve the toughness and corrosion resistance, eliminate the pressure and softening, and promote the continuous processing or formation of the aluminum alloy, it is necessary to carry out the solution treatment of the aluminum alloy, that is, the partial solution of the heat-resistant aluminum alloy temperature, and then warm it so that all phases dissolve completely, forming a uniform solid solution, and then rapidly cool (i.e., quench) to fix the high temperature solid solution. Obtain a supersaturated solid solution in preparation for aging.
After heat treatment, the plasticity of alloy forgings is reduced after timely treatment, and the strength and hardness are significantly improved. In actual production, aluminum alloy forgings usually need to be heated to a certain temperature and maintained for a certain period of time after quenching, that is, artificial aging.
When forging aluminum alloy materials, aluminum alloy parts that require multiple deformations at the forging temperature usually require multiple heating. At the same time, after forging, the forging needs dissolution treatment and artificial aging, so that the aluminum alloy parts need to be heated many times during the forging process, which increases the actual production cycle and production cost.
The advantages of forging are light weight, which is 20% lighter than cast wheels of the same size; it adopts physical integrated forging, which has the characteristics of high density and high strength; the forging size is accurate and the processing volume is small; it can make more beautiful shapes, and the spokes can Very thin and beautiful.
The Benefits Of Aluminum Forging
The thermal conductivity of aluminum alloy is 3-4 times that of steel. Its advantage is that the blank must be preheated, and it can be directly installed in a high-temperature furnace for heating. If it is too large, the deformation will be uneven, resulting in local critical deformation, which is easy to cause local coarse grains of the forgings, and the forgings will be uneven.
Aluminum alloys, especially aluminum-manganese alloys with extrusion effect, and the common coarse-grained rings on the surface of extruded bars may be related to the rapid heat dissipation and large friction on the surface of the blank, and the uneven deformation of the inner and outer layers falls into the critical deformation zone. To prevent the heat from dissipating too quickly, the mold and tools in contact with the workpiece must be preheated to a temperature of 300°C or higher.