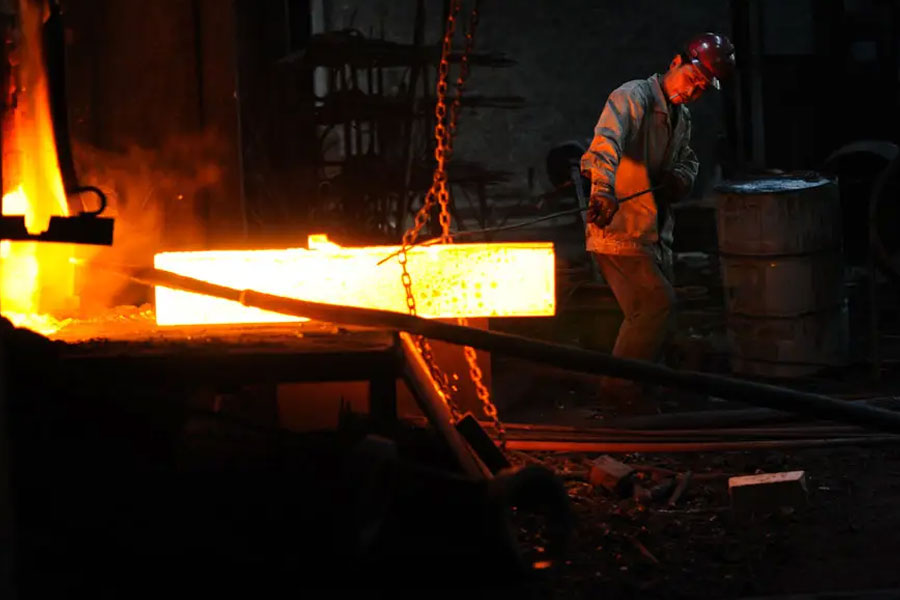
Die forgings have many closed sections, the distance between two ribs is short, the ribs are thin, the distance between two ribs and the thickness of the web are large, and the surfaces of many parts are not processed. Because the ribs of die forgings are much thinner, folding problems often occur at the intersection of thin ribs and webs and the connection between ribs and edge strips in production. Folding on die forgings destroys its continuity. Because it weakens the section, or fatigue cracks occur due to stress concentration during use, which greatly reduces the bearing capacity of forgings. Ribs are generally used to give rigidity or provide installation or link surfaces for other parts, so as to prevent folding defects.
Analysis On Folding Defect Position And Cause Of Aluminum Alloy Die Forgings
1.1 the folding position of die forgings can be seen from the structure and shape of forgings. In production, folding mostly occurs in the web, reinforcement and edge strip of forgings.
1.2 causes of folding defects
① The raw material design is unreasonable, resulting in differences in metal distribution. The forging process selection diameter is 180mm × 420mm long bar, squared according to the secondary multi-party section until 120mm × 180mm × 480mm, and then the middle part is elongated, and then finally pressed and formed on a 50 hydraulic press. It can be seen from its shape that the upper and lower ribs are symmetrical, although the shape of the blank is close to that of the forging, as shown in Figure 1.
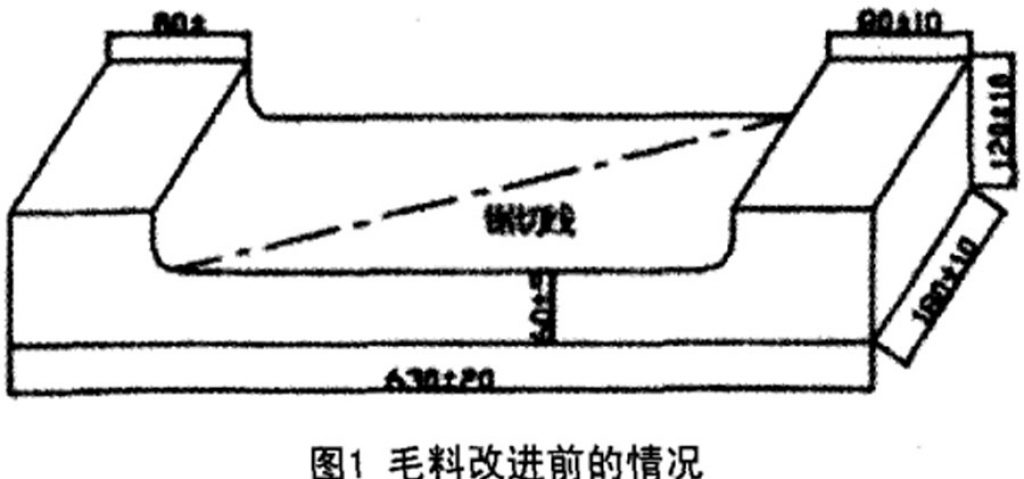
However, it can be seen from Figure 1 that the upper part of the forging blank and the bottom metal are uneven, the bottom metal distribution is large, and the height is not enough. The forging is symmetrical from top to bottom. During molding, the upper rib is filled with the mold cavity, and the lower metal is not filled. With the deformation, a cavity is generated in the upper part of the fillet in the mold cavity, where the metal and the lower part meet and fill, resulting in folding.
② From the analysis of the fillet radius of the connecting part between the web and the reinforcement, because the fillet radius is small, in the die forging, after the two reinforcements are filled, the upper and lower molds keep closing, and the surface metal passes through in the direction of less resistance, flows into the burr groove, and drives the surface metal to flow out, so that the reinforcement and the web are stacked together to produce folding.
③ When considering the molding from the metal flow direction, the metal filling cavity does not flow close to the fillet wall. Leave the fillet to make the metal contact with the opposite side wall first, and then with the bottom, and the metal backflow occurs to the fillet, which makes the positive flow coincide with the backflow metal surface, and then form a fold.
④ The wound was not completely repaired after the last molding, and the folding was not quickly repaired to make it enter the next molding, so that there were folds inside and outside the forging.
1.3 Solutions to folding defects
- ① Change the raw material of forgings to the selected diameter of 170mm × 280mm long bar is drawn on the drawing die, and the drawn head end is diameter (170 × 80 + 10) mm, the tail is flattened to 70 + 5I “~ 11ti thick. When the newly improved wool is selected for molding, it can be seen that the upper and lower metals are uniform, and the metal deformation is relatively uniform in the molding process. The rounded corner at the elongated part of the rod will transition smoothly. During molding, the flow resistance in the vertical direction of the parting is small, and no cavity can be generated in the upper part of the rounded corner in the cavity, so that the metal can fill the cavity evenly.
- ② Increase the fillet radius on the rib and web and the convex fillet radius on the mold, so that the mold cavity is evenly filled during metal molding, the flow resistance is reduced, and the excess metal will flow into the burr groove along the shape of the mold cavity.
- ③ There is no folding on the surface of the forging after the improved process, and the streamline is distributed along the forging, which meets the drawings and acceptance standards.
Folding defects of shaft forgings
Most of the forgings are shaft forgings, and the forming die is a drop die, which is composed of upper and lower parts. In forging, the forgings rotate around the axis without flash, such as clamping drop die and straightening drop die. The characteristic of die drop forming is that the lateral flow of metal is restricted by the side pressure of the die, so that the metal extends along the axis. Compared with free forging, the elongation rate is increased by ~ 1120% ~ 40%. At the same time, the internal longitudinal crack can also be prevented by the stress condition during internal drawing. In production, it is found that folding defects often occur at the step when the step shaft forging is forged with a general drop die.
2.1 folding defect problem the following is the process of half shaft forging, so as to explain the defects in the process of forming step shaft and the solution after die improvement. The forming steps of half shaft are as follows:
- The shoulder diameter is 130mm;
- Lengthen both ends to 130mm in diameter and form by free forging;
- Shoulder diameter at one end: 118mm;
- Lengthen one end to 115mm in diameter and free forging;
- Shoulder diameter 108mm;
- Lengthen the other end to 105mm in diameter and free forging;
- Trimming and straightening forming, straightening and falling die.
When using the falling die, folding defects are easy to occur in steps ①, ③, ⑤ and ⑦, especially the step of straightening the falling die.
Problem Analysis
Now take the step of straightening the falling die as an example to analyze the causes of defects and process improvement. Steps are generated at different parts of the falling mold cavity, and their height is determined in combination with the diameter difference, which prevents the steps from severe deformation and poor flow of metal in the forging process. When the upper and lower modules are closed, the fillet is set on the cavity to avoid stress concentration and smooth flow, and a step gap is generated at the contact step, which further affects the metal flow. In this way, at the step, except that most of the metal flows according to the tooling to produce steps, the rest of the metal has poor flow due to the change of diameter, and some of it flows into the gap between the upper and lower modules, forming a “flash” like that during die forging. During the rotary forging of the forging, the remaining metal is bent and attached to the surface of the forging due to its thin thickness. When further forging, it will be stuck in the forging to form a fold. As shown in (turn down page 1o5) (continued from page 1o3), there are two reasons for folding defects during ordinary die dropping: one is the steps on the cavity due to different diameters; The second is the fillet of the cavity. Analyze these two factors:
- The fillet of the cavity cannot be cancelled;
- Folding began to appear at the junction of the module, indicating that the steps close to its contact part are the main cause of folding.
2.3 problem solving modify the tooling to solve the folding problem of shaft forgings from the root. At the step of the falling die, two tangents are set in the tangential direction of the small-diameter circular arc to be tangent to the large-diameter fillet. In this way, the steps existing in the contact part of the module are partially eliminated and the shape change is slowed down. When the module is closed, a cavity containing the remaining metal is generated at the fillet, not the original step gap. When the remaining metal is shunted to this part during forging, there is no flash, but a prismatic block. When the forging is rotated and forged, this part of the remaining metal is prismatic, so it is not bent first and then folded due to its thickness. Instead, it is roughened and forged flat, and then melted into the inner part of the forging to form a whole without folding defects.
3 folding defects of bending forgings bending forgings are commonly used structural forgings, mainly including connecting rod, crankshaft and pipe joint. Most defects of this kind of forgings are the folding of the corner transfer part. When the forging streamline should be distributed along the direction of parts, this kind of folding is restricted by the shape of forgings, especially when the bending angle is less than 110. Folding is difficult to avoid.
3.1 part shape and defect location the forging material is stainless steel, the equipment used is friction press, and the process is bending blank making, open die forging and cold correction. The defect location and depth have this feature: the location is where the bending angle meets the platform. After polishing, the depth of the defect is 1-2mm. After sectioning and inspection, it is determined that the nature of the defect is folding.
At this time, there is a problem that the flow of the material towards the converging end of the die cavity will increase when the material is bent to the outer part of the die forming table, and if there is a difference between the filling end of the die and that of the die forming table, there will be a wrinkle when the material is bent to the converging end of the die forming table, Therefore, folding occurs.
3.3 measures to solve defects: this measure should be taken to solve the causes of defects. The bending process is a key step to cause folding. According to the experiment, when the temperature and striking force are appropriate, the bending angle of this material after bending exceeds 120., When the bending radius exceeds 8mm, the blank generally does not appear wrinkle. Comprehensively analyze the placement and material of the forging, and change the bending angle from 110. Change to 115., The inner radius of bending is changed from 5mm to 10mm, so as to reduce the possibility of bending folds and eliminate the hidden danger of folds developing into folds. In addition, the design of bending groove is very important in the design of bending die. After the bar is bent, elliptical deformation will appear in the deformation area. Pay attention to whether the section is sunken after bending. If so, timely adjust the design of bending groove and increase the size of inclination angle from 135. Add to 150.
4 Conclusion
Through the analysis of the causes of forging folding, and then the improvement of forging raw materials and the change of die size, the forging size is good, the forging surface and macrostructure are not folded, the mechanical properties of the forging meet the standard requirements, and its quality is stable.
For example, the improved design of step shaft and tooling has been used in production. All die drop designs have basically solved the problem of step shaft folding defects. For the folding defects of bending forgings, the important thing is that the forging process and die design must be reasonable and appropriate.